Contents
OWNING AND READING MOST IMPORTANT BOOKS IN CEMENT INDUSTRY + MANUALS AND NOTES AND SHEETS FROM THE MOST SUCCESSFUL PLAYERS IN CEMENT INDUSTRY WILL CHANGE YOUR CAREER AND WILL MAKE YOU REACH MANAGERIAL POSITIONS FASTER , KINDLY CLICK HERE TO GET EVERYTHING
Kiln Control and Operation
TO DOWNLOAD THE MOST IMPORTANT BOOKS , MANUALS , OPERATION NOTES , FORMUFLAS , EXCEL SHEETS CLICK HERE NOW !!
SUMMARY
Control Parameters
The most important control parameters in any type of kiln system are:
- Burning Zone Temperature (as an indicator for the produced clinker quality)
- Back End Temperature (as an indicator for the raw meal preparation, which is mainly drying, heat up and calcination)
- Oxygen concentration of the kiln exit gas (as an indicator for the efficiency of combustion)
- In case of precalciner systems: Temperature and oxygen concentration at precalciner outlet
- In case of a grate coolers: Bed height of the clinker layer on the grate
Control variables
The most important control variables that are adjusted to maintain the previous control parameters in a certain allowed range are:
- Fuel rate to the kiln
- Material feed rate to the kiln
- Draft in the kiln
- Kiln speed
- In case of precalciner systems: Fuel rate and draft in the precalciner
- In case of a grate coolers: Grate speed
Objectives of kiln operation
The operation of a kiln system has to meet the following basic requirements:
- Protection of equipment and personnel at all times
- Consistently good clinker quality
- Smooth and stable operation
- Maximum thermal efficiency
- Maximum production rate
1. INTRODUCTION
The different kiln systems can be distinguished by the moisture content of the raw material, which is fed to the kiln system. The different process types are:
- Wet process 30-40 % Moisture
- Semi wet process 17-21 % Moisture
- Semi dry process 10-15 % Moisture
- Dry process < 1 % Moisture
Although each type of process has its own particular operation parameters, the raw meal has to undergo similar chemical and physical reactions until the clinker finally leaves the kiln system.
The basic reactions are:
- Drying of the raw meal
- Heat up of the material
- Calcination
- Formation of the clinker minerals
- Cooling of the clinker
The main difference between the different types of process lies in the required time and energy, each reaction needs to be completed.
Therefore the operating range of the different control parameters is varying from one kiln system to the other. The same applies to the response time as well as to the frequency and magnitude of any control variable adjustment.
Nevertheless certain basic rules are applicable for all types of kiln systems. They are presented in the following and shall give an elementary concept of kiln operation.
1. CONTROL PARAMETERS
Kiln systems normally are equipped with a great number of instruments, sensors and measuring devices.
Some of them are for information purpose only (e.g. if a flap is opened or closed), others to detect dangerous situations (e.g. cyclone blockages), but only few of them are continuously used for kiln operation.
Those measured values that are the most important for kiln operation are herein called the control parameters. To keep the control parameters close to a certain target control variables (or actuators) are manipulated.
The most important control parameters that are looked at during kiln operation are:
- Burning Zone Temperature (as an indicator for the produced clinker quality)
- Back End Temperature (as an indicator for the raw meal preparation, which is mainly dryout, heat up and calcination)
- Oxygen concentration of the combustion gas at the kiln inlet or the preheater (as an indicator for the efficiency of combustion and the gas atmosphere inside the kiln)
- In case of precalciner systems: Temperature and oxygen concentration of the exhaust gas at the precalciner outlet
- In case of a grate cooler: Bed height of the clinker bed
1.1 Location of the control parameters and variables
The location where the different control parameters are measured and some typical target values are given below. The control variables, which are adjusted to keep the parameter close to target, are shown also for the different types of kiln systems.
1.1.1 Wet kiln
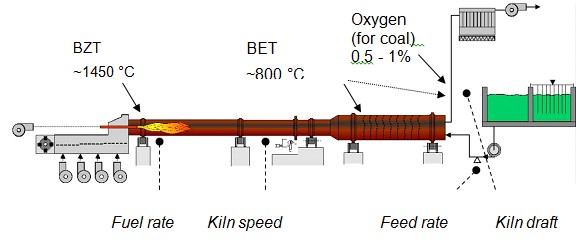
Figure 1: Control parameters and variables of a wet kiln
1.1.1 Lepol kiln
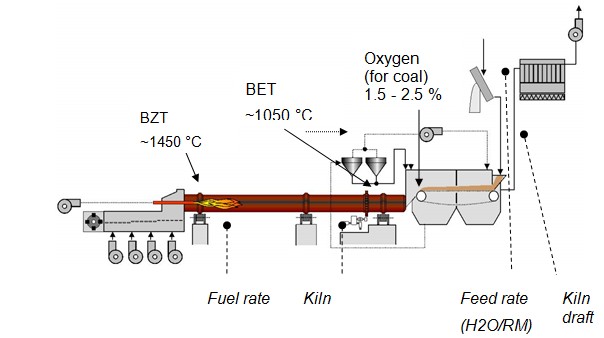
1.1.1 Preheater kiln
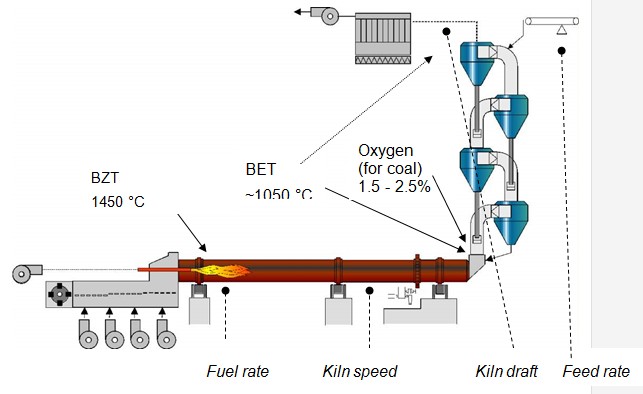
1.1.1 Precalciner kiln
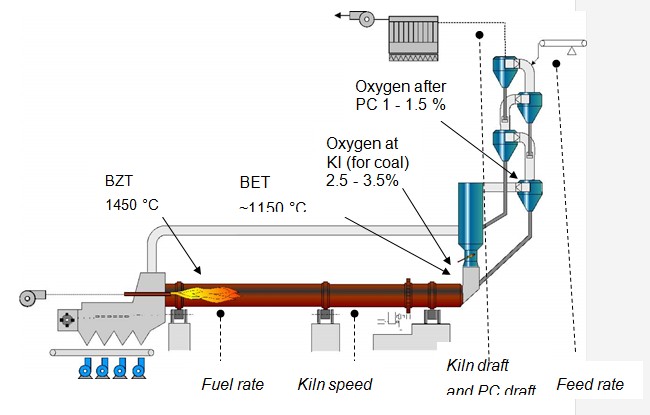
1.1 Burning Zone Temperature (BZT)
The BZT determines, how well the clinker is burned and how complete the transformation from C2S to C3S is. When the clinker is leaving the burning zone it should not have more than ~1.5% and not less than ~0.5% of uncombined CaO or free lime (which roughly corresponds to a liter weight of about 1250-1350 g/l).
The periodically measured free CaO (or the liter weight) is the main indicator to state, if the actual BZT target is adequate or if it has to be increased or lowered.
Due to changes of the raw meal composition an alteration of the BZT target can be required now and then, since burnability of the raw material changes with fluctuations of the LSF, SR, magnesia and alkali content among other factors. A change in the flame characteristics, which can result from the use of multiple fuels or varying combustion conditions has a similar impact and therefore may also require an alteration of the BZT target.
Variations of the BZT target are made only over a long-term period, in the same way as the free CaO (or liter weight) is measured normally only on a one or two hourly basis.
The actual BZT must be measured to determine, if a deviation between the temporary target and the actual BZT exists.
Since kiln operation is a dynamic process, deviations are quite frequent and of a short-term character.
Several indicators are used to determine the BZT and they are listed below.
Most do not explicitly express an absolute temperature but they give sufficient information to establish, if the BZT increased or decreased compared to an earlier defined target. This means they give the short-term trend of the control parameter BZT. This helps to estimate the probable free CaO (or the liter weight) and must bridge the time until the actual clinker analysis is available.
1.1.1 Pyrometer reading
The radiation of clinker and coating in the burning zone has a relation to its temperature. Therefore the BZT can be determined by measuring the intensity or the color of this radiation.
A rough temperature – color correlation is given below (visible range):
Lowest visible red to dark red 475-650 °C
Dark red to cherry red 650-750 °C
Cherry red to bright red 750-850 °C
Bright red to orange 850-900 °C
Orange to yellow 900-1100 °C
Yellow to light yellow 1100-1350 °C
Light yellow to white 1350-1550 °C
By measuring the color of the burning zone and not only the radiation intensity, the reading is less influenced by disturbances like the dust load of the secondary air and others.
Therefore modern pyrometers and kiln cameras mainly measure the color and not the intensity of radiation.
1.1.2 NOx of the exhaust gases
The NOx that is produced during combustion varies according the temperature of the flame and of the gases of the burning zone. The hotter the flame is the more NOx is produced during combustion and vice versa.
When BZT is deduced from the NOx content of the exhaust gases, the oxygen and CO concentration in the exhaust gases have to be considered also, since CO reduces and oxygen promotes the formation of NOx.
A further factor influencing NOx formation is the type of fuel burned. If the fuel mix changes, the quantity of NOx produced may change too (especially when burning alternative fuels).
1.1.1 Kiln torque
The burning zone shifts upwards and gets longer, if the BZT rises.
A higher BZT produces more liquid phase in the clinker.
The diameter of the clinker balls increases and the granulation of the raw meal in the kiln starts earlier. Therefore more and bigger clinker balls have to be moved inside the kiln when the BZT is increasing.
At the same time, the material bed in the kiln is lifted up more, which moves the center of gravity away from the kiln axis.
The different granulation of the clinker and the changing angle of repose increase the required torque to turn the kiln, if BZT rises.
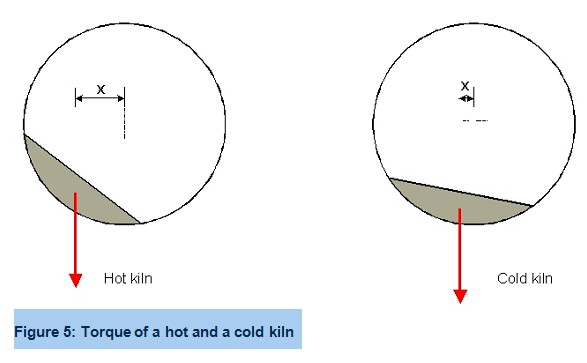
This kiln torque is proportional to the current of a DC – drive and proportional to the quotient kiln power / kiln speed in case of an AC – drive or a hydraulic drive.
A changing coating situation in the burning zone strongly influences the kiln torque (as more as lower the L/D ratio of the kiln). As a result the kiln torque can change significantly on a long-term basis without any change of the BZT. Therefore the kiln torque signal in most cases only serves as a short-term indication of the BZT. Short-term is defined as up to 12 hours. Torque is a very useful indicator of kiln conditions relative to its trend.
1.1.1 Secondary Air Temperature (SAT) or Tertiary Air Temperature (TAT)
Kilns with a grate cooler, which are equipped with a reliable SAT or TAT measurement device, often use SAT or TAT as an indicator for the BZT.
The higher the BZT, the hotter the released clinker and the higher SAT or TAT (and vice versa).
Nevertheless SAT and TAT are influenced by a number of other effects (clinker granulometry, cooler operation, etc.), therefore not in all kilns can a clear correlation between BZT and SAT or TAT be given.
1.1.2 Position of the dark feed (valid only for pure natural gas flames)
If the visibility inside the kiln does permit (little dusty, flame shape, etc.), the calcined hot meal can be seen as a dark flush, when entering the burning zone. An area can be determined, where this meal, floating like water starts to form liquid phases and where it transforms to solid clinker balls.
The position of the area where this transformation takes place is an additional indicator of the BZT.
If this area shifts downwards, the BZT is falling and vice versa.
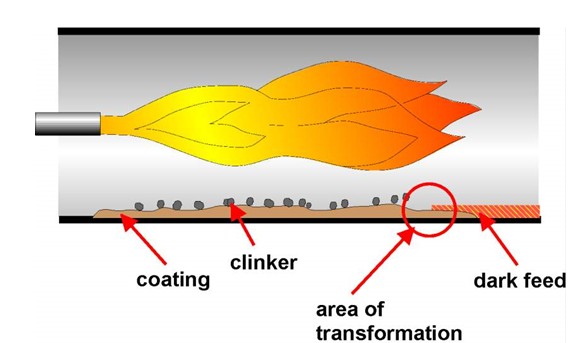
1.1 Back End Temperature (BET)
The term BET refers to the temperature of the exhaust gas at the kiln inlet in case of kilns with a preheater and to the intermediate gas temperature (before the chain section), if the kiln is equipped with chains. The BET depends on the type of system and the L/D – ratio of the kiln. It ranges from ~800 °C in wet kilns (before the chain section) up to ~1200 °C in AS precalciner kilns.
If a reliable temperature measurement at the kiln inlet (kilns with preheaters) or before the chain section (kilns with chains) is not available, frequently the preheater exit temperature (kilns with preheaters) or the kiln inlet temperature (kilns with chains) is used.
The BET is an indicator of how well the hot meal is prepared, when entering the kiln (or when passing the intermediate measuring point, in case of kiln systems with chains).
Before the meal is finally clinkerized in the burning zone, it has to undergo dryout, calcination (release of CO2) and to a minor extend also reactions like structural modifications and the formation of intermediate products like C12A7 or CA).
The higher the energy demand for intermediate reactions in the kiln, (which depends mainly from the type of process), the more important is a proper control of the BET.
Hence the BET in a wet kiln is more critical (90-100% calcination missing) than in an air separate precalciner kiln (~10% calcination missing).
The BET reacts as slower to any control variable adjustment as longer the kiln (higher L/D ratio) and as more energy is consumed in the kiln for the intermediate reactions before clinkerisation.
Ideally the material should always have the same degree of preparation, but due to the kiln operation itself and normal fluctuations of the raw material properties, fuels, ambient conditions and others, this is not the case.
Variations in the raw material are first observed through the BET, thereby indicating early the future impact on the BZT.
If all other parameters remain constant and the BET drops, this is evidence that all reaction zones shift downward and vice versa.
If the zones within the kiln shift either down or up, the BZT will decrease or increase consequently afterwards also, if no counter measures are taken earlier.
1.2 Oxygen control
For a good combustion of the fuels a certain amount of excess air is required.
The quantity of excess air is determined by measuring the oxygen content of the exhaust gases. Proper control of the oxygen level is crucial for good combustion and a high thermal efficiency.
Typical oxygen ranges (at the kiln inlet) for the most common kiln systems are given in the following table. The required oxygen level depends on the type of kiln system but also strongly on the type of fuel being used (e.g. gas needs less excess air than coal or solid AFR).
A further important influence to the oxygen level is the amount of sulfur, chlorine and alkali within the kiln system. Therefore the higher oxygen levels within the given ranges are chosen, if sulfur volatilization is a problem.
Gas | Fuel oil | Coal | Petcoke Solid AFR | |
Wet kiln | 0.5 – 1.0 % | 1.0 – 2.0 % | 1.5 – 2.0 % | 2.0 – 2.5 % |
Lepol kiln | 1.0 – 1.5 % | 1.5 – 2.0 % | 1.5 – 2.5 % | 2.0 – 3.0 % |
Preheater kiln | 1.0 – 1.5 % | 1.5 – 2.0 % | 1.5 – 2.5 % | 2.0 – 3.0 % |
Inline PC kiln | 2.5 – 3.0 % | 2.5 – 3.0 % | 2.5 – 3.5 % | 2.5 – 4.0 % |
Separate PC kiln | 1.0 – 1.5 % | 1.5 – 2.0 % | 1.5 – 2.5 % | 2.0 – 3.0 % |
Table 1: Typical oxygen levels at the kiln inlet (dry gas)
In most kiln systems the required amount of excess air is slightly above the point where the flame temperature would be highest due to sulfur, chlorine or alkali situation.
Therefore a slight reduction of the amount of excess air increases the flame temperature a little.
Extremely low excess air (or oxygen) reduces the flame temperature, which lengthens the flame (postcombustion) and lowers the fuel efficiency. Additionally sulfur and alkali volatilization is enhanced, which may lead to build up and incrustation problems within the kiln system.
Too much excess air (or oxygen) cools the flame too and leads also to a poor thermal fuel efficiency due to the deteriorating heat transfer. Since the total gas flow is increased, the kiln internal and external dust cycles also increase.
Hence lower oxygen levels are chosen, if sulfur volatilization is not problematic.
As a general rule applies, that at the minimum permissible oxygen level no notable CO is formed (i.e. < 0.05 % at kiln inlet).
1. CONTROL VARIABLES
In the proceeding paragraph the main control parameters used for kiln control were presented.
Those parameters must be kept in a narrow range closed to target, in order to run the kiln in a smooth and efficient manner. Generally speaking the smaller the deviations of the parameter from the target, the better the kiln control.
To keep the control parameters close to target it is generally necessary to make adjustments to the control variables.
The main control variables are (excluding precalciner systems):
- Fuel rate to the kiln
- Material feed rate to the kiln
- Kiln draft
- Kiln speed
In the following the effect of any adjustment made to one of the four kiln control variables is shown. To keep the normally relatively complex relations simple it is assumed, that the adjustment is done only to one variable at a time (the others remain untouched) and that the adjustment is so small, that none of the control parameters deviates far from target.
1.1 Fuel rate to the kiln
When increasing the fuel rate into the kiln:
- BZT increases
- BET increases
- Oxygen concentration decreases
(A decrease of the fuel rate has the inverse effect).
More energy is introduced into the system, therefore the BZT and the BET rises. Oxygen level drops, since part of the excess air is consumed for the combustion of the extra fuel.
Of course, the above applies only, if the combustion does not takes place under reducing conditions.
1.2 Feed rate to the kiln
When increasing the material feed rate into the kiln:
- BZT decreases
- BET decreases
- Oxygen concentration decreases
(A decrease of the feed rate has an inverse effect).
When more feed is introduced into the kiln system the temperature starts to drop first at the back end. After the higher amount of feed has reached the burning zone, the BZT starts to decrease also.
The extra feed releases additional H2O and CO2. The additional amount of gas from the meal reduces the quantity of combustion air (and thus of excess air), since the amount of exhaust gas remains (almost) constant. This leads to a decrease of oxygen in the exhaust gas.
1.3 Kiln draft
When increasing the draft in the kiln:
- BZT decreases
- BET increases
- Oxygen concentration increases
(A slight decrease of the draft has an inverse effect. If combustion takes place under reducing conditions (too little excess air) the BZT drops again and BET rises (see chapter 2.4).
When the kiln draft rises, more (and slightly colder) secondary air is pulled into the kiln and through the burning zone. This decreases the flame temperature and as a result the BZT drops.
Although the amount of heat supplied to the kiln system is somewhat higher (more secondary air), less heat is released in the burning zone (lower flame temperature results in reduced heat transfer) thus the BET rises.
The higher kiln draft increases both, the oxygen concentration and the volume of the exhaust gases.
1.4 Kiln speed
When increasing the speed of the kiln:
- BZT decreases (temporarily)
- BET decreases (temporarily)
- Oxygen decreases (temporarily)
(A decrease of the kiln speed has the inverse effect)
When the kiln speed is increased, the meal advancement is faster. All reaction zones shift temporarily downwards, which causes the BET and the BZT to drop.
Since more meal enters temporarily the drying and the calcining zone (same effect as an increased feed rate), a higher amount of H2O and CO2 is released which leads to a drop in the oxygen concentration.
Those effects are only temporary, since a higher kiln speed at a fixed feed rate reduces the filling degree in the kiln. Once the kiln filling degree has been lowered in the entire kiln (all material, that was in the kiln, when the speed change was made, has left the kiln), BZT, BET and oxygen recover.
Remark:
In almost all kiln operation strategies the kiln speed depends on the kiln feed rate. The objective is to keep the filling degree in the kiln constant. Thus the kiln speed is under normal operation conditions is not an independent variable, but adjusted in tandem with the kiln feed rate.
In certain upset conditions (especially the dreaded hot meal rush), the kiln speed has to be reduced that much that a parallel reduction of the kiln feed would produce an overheating of the back end. In these situations, a compromise between increased filling degree and BET must be made (under this situation, the so-called cycling can occur).
2. CONTROL STRATEGY
2.1 General remarks
As seen before an adjustment to only one of the control variables has an impact on all three control parameters.
To keep all control parameters within a certain range close to target it is normally necessary to make adjustments to more than one control variable.
But in doing so, the correction of one particular control parameter can increase the deviation of an other.
As a result a compromise must be found that reduces the weighted average of all parameter deviations to a minimum.
The weight (degree of importance) of each particular control parameter depends on the type of system and the particular kiln. In a precalciner kiln for example the BET is less critical than in a wet kiln. Therefore the influence of the BET is less weighted in a precalciner kiln than in a wet kiln.
The selection of the control variables used to bring one or more control parameter that are out of range back to normal depends on the overall view of all control parameters.
In the following an example of a kiln operation strategy is presented, which describes the most typical actions, which may be taken for all types of kiln systems. Certain modifications of this strategy may be necessary in particular cases, since each kiln behaves differently and has dissimilar preconditions.
A very important factor herein plays the ability to make positive changes to the control variables. In many kilns a bottleneck exists, that does not allow any positive change to one of the control variables, once nominal capacity has been reached (e.g. an ID fan that runs already with maximum speed or with the damper completely opened). This consequently may require an alteration of the presented strategy.
The purpose of this strategy is to understand the principles of kiln operation and may not be directly applicable on all kiln systems.
2.2 Possible kiln parameter conditions
It is assumed that the three kiln parameters BZT, BET and Oxygen at kiln inlet can be attributed to one of the following states (although transitions are fluid), which are:
- Inside the desired range, which means k.
- Above the desired range, which means high
- Below the desired range, which means low
The desired range for the three control parameters typically is as followed:
BZT | BET | Oxygen | |
Wet kiln | Target +/- 20 °C | Target +/- 10 °C | Target +/- 0.3 % |
Lepol kiln | Target +/- 20 °C | Target +/- 15 °C | Target +/- 0.5 % |
Preheater kiln | Target +/- 20 °C | Target +/- 15 °C | Target +/- 0.5 % |
Inline PC kiln | Target +/- 20 °C | Target +/- 20 °C | Target +/- 0.7 % |
Separate PC kiln | Target +/- 20 °C | Target +/- 20 °C | Target +/- 0.5 % |
Table 2: Desired range of the different control parameters
Combining the three control parameters and their respective state in any combination, leads to 3^3=27 possible conditions. These 27 basic conditions are shown graphically below in the so-called “decision tree”.
2.3 Decision tree
Based on the 3 possible conditions of the 3 control parameters, the following decision tree is built, which covers all 27 possible states.
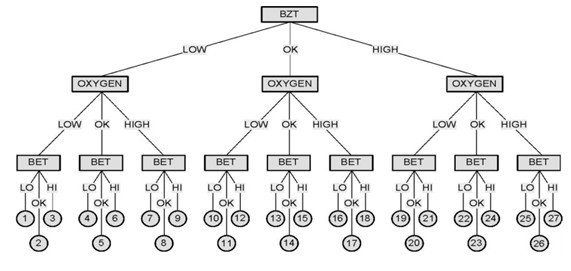
1.1 Counteractions
For each of the possible 27 states a particular action (control variable adjustment) is described, to bring the control parameters back to target, which is the desired state 14.
The counteractions apply under the assumption that no bottleneck exists.
Although it is not always explicitly mentioned, the magnitude of a possible deviation plays a great role, since it influences the intensity of counteraction. Any adjustment to the control variables must be more or less pronounced, according the degree of parameter deviation from the target. Otherwise the correction of the kiln parameters is either insufficient or too strong, which results in a weak response or in an overshoot of the parameter reaction (creating a cycling effect).
In kiln systems, where the BET is of minor importance, mostly the BZT and the oxygen establish the actions. This means a certain deviation from the BET target is temporarily accepted, if this helps to maintain a high productivity and as long as the overall kiln condition does not suffer. If allowed to continue for prolonged periods, elevated BET may result in increased condensation of circulating elements in difficult to reach areas. This can cause plugging and possible kiln stoppages and must be avoided.
The actions to be usually taken are (the actions to be taken lay more emphasis on a stable kiln operation than on maximum productivity):
Case | Condition | Action | Reason | ||||||
1 | BZT | low | When BZT is slightly low: | ||||||
OXYGEN | low | 1 | increase kiln draft | increase oxygen and prepare for step 2, increase BET | |||||
BET | low | 2 | increase fuel rate | increase BZT and BET, bring oxygen back to normal | |||||
When BZT is very low: | |||||||||
1 | increase kiln draft | increase oxygen and prepare for step 2, increase BET | |||||||
2 | increase fuel rate | increase BZT and BET, bring oxygen back to normal | |||||||
3 | decrease kiln speed | increase BZT and BET even more | |||||||
4 | decrease feed rate | maintain kiln filling degree constant | |||||||
2 | BZT | low | 1 | increase kiln draft slightly | increase oxygen, increase BET to prepare for step 2 | ||||
OXYGEN | low | 2 | decrease fuel rate | increase oxygen even more, bring BET back to normal | |||||
BET | o.k. | 3 | decrease kiln speed | increase BZT | |||||
4 | decrease feed rate | maintain kiln filling degree constant | |||||||
3 | BZT | low | 1 | decrease fuel rate | increase oxygen and prepare for step 2, decrease BET | ||||
OXYGEN | Low | 2 | decrease kiln draft | decrease BET | |||||
BET | High | 3 | decrease kiln speed | increase BZT | |||||
4 | decrease feed rate | maintain kiln filling degree constant | |||||||
4 | BZT | Low | When BZT is slightly low: | ||||||
OXYGEN | o.k. | 1 | increase kiln draft | increase BET, increase oxygen to prepare for step 2 | |||||
BET | Low | 2 | increase fuel rate | increase BZT and BET | |||||
When BZT is very low: | |||||||||
1 | increase kiln draft | increase BET, increase oxygen to prepare for step 2 | |||||||
2 | increase fuel rate | increase BZT and BET | |||||||
3 | decrease kiln speed | increase BZT and BET even more | |||||||
4 | decrease feed rate | maintain kiln filling degree constant and increase BET | |||||||
5 | BZT | Low | When BZT slightly low and oxygen slightly high, but still o.k.: | ||||||
OXYGEN | o.k. | 1 | increase fuel rate | increase BZT | |||||
BET | o.k. | When BZT very low: | |||||||
1 | increase kiln draft slightly | increase oxygen and prepare for step 2 | |||||||
2 | increase fuel rate slightly | increase BZT | |||||||
3 | decrease kiln speed | increase BZT more | |||||||
4 | decrease feed rate | maintain kiln filling degree constant | |||||||
6 | BZT | Low | When BZT is slightly low and oxygen is slightly high, but still o.k.: | ||||||
OXYGEN | o.k. | 1 | decrease kiln draft | increase BZT and decrease BET | |||||
BET | High | When BZT is very low: | |||||||
1 | decrease fuel rate | decrease BET, increase oxygen to prepare for step 2 | |||||||
2 | decrease kiln draft | decrease BET, bring oxygen back to normal | |||||||
3 | decrease kiln speed | increase BZT | |||||||
4 | decrease feed rate | maintain kiln filling degree constant | |||||||
7 | BZT | Low | When BZT is slightly low: | ||||||
OXYGEN | high | 1 | increase fuel rate | increase BZT and BET, decrease oxygen | |||||
BET | low | When BZT is very low: | |||||||
1 | increase fuel rate | increase BZT and BET, decrease oxygen | |||||||
2 | decrease kiln speed | increase BZT and BET | |||||||
3 | decrease feed rate | maintain kiln filling degree constant | |||||||
8 | BZT | low | When BZT is slightly low: | ||||||
OXYGEN | high | 1 | increase fuel rate | increase BZT, decrease oxygen | |||||
BET | o.k. | When BZT is very low: | |||||||
1 | increase fuel rate | increase BZT, decrease oxygen | |||||||
2 | decrease kiln speed | increase BZT | |||||||
3 | decrease feed rate | to maintain kiln filling degree constant | |||||||
9 | BZT | low | When BZT is slightly low: | ||||||
OXYGEN | high | 1 | increase fuel rate | increase BZT, decrease oxygen | |||||
BET | high | 2 | decrease kiln draft | decrease BET and oxygen, compensate BET increase of step 1 | |||||
When BZT is very low: | |||||||||
1 | increase fuel rate | increase BZT, decrease oxygen | |||||||
2 | decrease kiln draft | decrease BET and oxygen, compensate BET increase of step 1 | |||||||
3 | decrease kiln speed | increase BZT | |||||||
4 | decrease feed rate | to maintain kiln filling degree constant | |||||||
10 | BZT | o.k. | 1 | increase kiln draft | increase oxygen, increase BET | ||||
OXYGEN | low | 2 | increase fuel rate slightly | compensate BZT decrease of step 1 | |||||
BET | low | ||||||||
11 | BZT | o.k. | 1 | increase kiln draft | increase oxygen | ||||
OXYGEN | low | ||||||||
BET | o.k. | ||||||||
12 | BZT | o.k. | 1 | decrease fuel rate | decrease BET, increase oxygen and prepare for step 2 | ||||
OXYGEN | low | 2 | decrease kiln draft slightly | decrease BET | |||||
BET | high | ||||||||
13 | BZT | o.k. | 1 | increase kiln draft | increase BET | ||||
OXYGEN | o.k. | 2 | increase fuel rate slightly | compensate oxygen increase and BZT decrease of step 1 | |||||
BET | low | ||||||||
14 | BZT | o.k. | When this condition persists: | ||||||
OXYGEN | o.k. | 1 | increase kiln draft | increase oxygen to prepare for step 2 | |||||
BET | o.k. | 2 | increase fuel rate | increase BZT to prepare for step 3 | |||||
3 | increase feed rate | increase production | |||||||
4 | increase kiln speed | to maintain kiln filling degree constant | |||||||
When this condition is only temporary: | |||||||||
1 | No action | ||||||||
15 | BZT | o.k. | When oxygen is slightly high, but still o.k.: | ||||||
OXYGEN | o.k. | 1 | decrease kiln draft | decrease BET | |||||
BET | high | When oxygen is slightly low, but still o.k.: | |||||||
1 | decrease fuel rate | decrease BET and prepare for step 2 | |||||||
2 | decrease kiln draft | decrease BET | |||||||
16 | BZT | o.k. | 1 | increase kiln draft slightly | increase BET, increase oxygen to prepare for step 2 | ||||
OXYGEN | high | 2 | increase fuel rate | increase BET, compensate BZT decrease of step 1 | |||||
BET | low | ||||||||
17 | BZT | o.k. | 1 | decrease kiln draft | decrease oxygen | ||||
OXYGEN | high | ||||||||
BET | o.k. | ||||||||
18 | BZT | o.k. | 1 | decrease kiln draft | decrease oxygen and BET | ||||
OXYGEN | high | 2 | decrease fuel rate slightly | decrease BET, compensate BZT increase of step 1 | |||||
BET | high | ||||||||
19 | BZT | high | When BZT is slightly high: | ||||||
OXYGEN | low | 1 | increase kiln draft | increase oxygen, increase BET | |||||
BET | low | When BZT is high: | |||||||
1 | increase kiln draft | increase oxygen, increase BET | |||||||
2 | increase kiln speed | decrease BZT | |||||||
3 | increase feed rate | to maintain kiln filling degree constant | |||||||
20 | BZT | high | When BZT is slightly high: | ||||||
OXYGEN | low | 1 | increase kiln draft | increase oxygen, decrease BZT | |||||
BET | o.k. | When BZT is high: | |||||||
1 | decrease fuel rate | increase oxygen, decrease BZT | |||||||
2 | increase kiln speed | decrease BZT | |||||||
3 | increase feed rate | to maintain kiln filling degree constant | |||||||
21 | BZT | high | When BZT is slightly high: | ||||||
OXYGEN | low | 1 | decrease fuel rate | decrease BZT and BET, increase oxygen | |||||
BET | high | When BZT is high: | |||||||
1 | decrease fuel rate | decrease BZT and BET, increase oxygen | |||||||
2 | increase kiln speed | decrease BZT and BET | |||||||
3 | increase feed rate | to maintain kiln filling degree constant | |||||||
22 | BZT | high | When BZT is slightly high: | ||||||
OXYGEN | o.k. | 1 | increase kiln draft | decrease BZT, increase BET | |||||
BET | low | When BZT is high: | |||||||
1 | increase kiln draft | decrease BZT, increase BET | |||||||
2 | increase kiln speed | decrease BZT and BET | |||||||
3 | increase feed rate | to maintain kiln filling degree constant | |||||||
23 | BZT | high | When BZT is slightly high: | ||||||
OXYGEN | o.k. | 1 | decrease fuel rate | decrease BZT | |||||
BET | o.k. | When BZT is high: | |||||||
1 | decrease fuel rate | decrease BZT | |||||||
2 | increase kiln speed | decrease BZT | |||||||
3 | increase feed rate | to maintain kiln filling degree constant | |||||||
24 | BZT | high | When BZT is slightly high: | ||||||
OXYGEN | o.k. | 1 | decrease fuel rate | decrease BZT and BET | |||||
BET | high | When BZT is high: | |||||||
1 | decrease fuel rate | decrease BZT and BET | |||||||
2 | increase kiln speed | decrease BZT and BET | |||||||
3 | increase feed rate | to maintain kiln filling degree constant | |||||||
25 | BZT | high | When BZT is slightly high: | ||||||
OXYGEN | high | 1 | increase kiln draft | decrease BZT, increase BET | |||||
BET | low | When BZT is high: | |||||||
1 | increase kiln draft | decrease BZT, increase BET | |||||||
2 | increase kiln speed | decrease BZT and BET | |||||||
3 | increase feed rate | to maintain kiln filling degree constant | |||||||
26 | BZT | high | When BZT is slightly high: | ||||||
OXYGEN | high | 1 | decrease fuel rate | decrease BZT | |||||
BET | o.k. | When BZT is high: | |||||||
1 | increase kiln draft | decrease BZT, increase BET to prepare for step 2 | |||||||
2 | increase kiln speed | decrease BZT | |||||||
3 | increase feed rate | to maintain kiln filling degree constant | |||||||
27 | BZT | high | When BZT is slightly high: | ||||||
OXYGEN | high | 1 | decrease fuel rate | decrease BZT and BET | |||||
BET | high | 2 | decrease kiln draft | decrease oxygen | |||||
When BZT is high: | |||||||||
1 | decrease fuel rate | decrease BZT and BET | |||||||
2 | decrease kiln draft | decrease oxygen | |||||||
3 | increase kiln speed | decrease BZT | |||||||
4 | increase feed rate | to maintain kiln filling degree constant |
The basic 27 counteractions apply to the kiln operation only and do not consider precalcining, Lepol preheater or grate cooler operation.
If a precalcination system is installed, additional control parameters have to be held on target.
The same applies for a grate cooler (which is the most common type of cooler and has the highest operational adjustability) and a Lepol preheater.
2. PRECALCINER CONTROL
The purpose of precalcining is to shift the reaction of calcination from the kiln upstream into a kiln external precalciner.
Although preheaters with secondary firing and air through precalciner belong to this group also, they are not considered further, since the fuel rate to the secondary firing or to the air through calciner is normally held constant and they do not provide particular control of the calcining degree at the kiln inlet. Also the amount of energy spent for precalcination is limited in those types (normally << 20 % of the total thermal energy).
The presented system is the air separate calciner, where the combustion air is not delivered through the kiln, but through a tertiary air duct.
In these precalciners, the meal is calcined almost completely (up to 90 %) and more than half of the total thermal energy (up to 60 %) is spent for this reaction.
It is the objective to calcine the meal as much and as uniform as possible.
This is the main operational advantage of an air separate precalciner, because it gives the possibility, to control the preparation of the meal completely independent from the kiln. Therefore the BET has little importance from an operational point of view.
2.1 Calcination temperature
In kiln operation the free CaO (or liter weight) determines the BZT target (control parameter), which is held close to target mainly by means of the fuel rate to the main burner (control variable).
Similarly in precalcining systems the calcination degree establishes the calcining temperature (control parameter), which then is held, close to target by the fuel rate to the calciner (control variable). This calcination temperature in calciner systems basically takes over the function of the BET of the other kiln systems.
A normal desired calcination degree in a precalciner system is around 90 %, which corresponds to a material temperature (or a calciner exit gas temperature) of 870-890°C.
A higher calcination degree is obtained with a higher calcination temperature, but at temperatures above 900°C already liquid phase starts to form, which leads to build-ups in the calciner and a restricted gas flow. Therefore excess temperatures are not desired.
From an operational point of view the following general rules exist to establish the calcining temperature and calcination degree:
– The higher the calcination temperature (and calcination degree), the more uniform is the calcination degree (since the gradient of the calcining curve decreases with increasing calcination temperature) and the more stable is consequently kiln operation, but the lower is the thermal efficiency of the precalciner kiln system, due to higher calciner and preheater exit temperatures.
– The lower the calcination temperature (and calcination degree), the less uniform the calcination degree (since the gradient of the calcining curve increases with decreasing calcination temperature) and the more sensitive is the calcination degree to fluctuations (disturbances) on rate and properties of precalciner fuel and kiln feed.
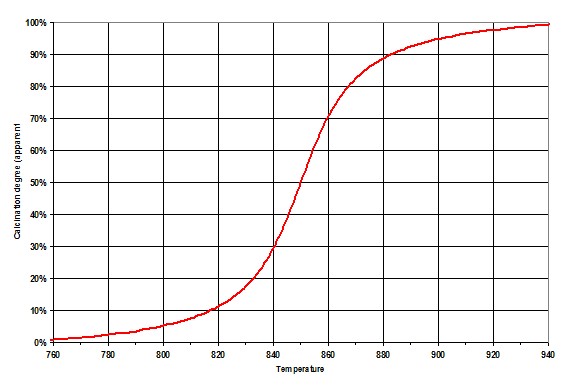
1.1 Oxygen control
The oxygen at the calciner outlet is controlled through the calciner draft, in the same way as the oxygen at kiln inlet is controlled by the kiln draft.
A normal target value for the oxygen after calciner (bottom cyclone exit) is 1 – 1.5 %.
In air separate calciner systems, the calciner draft is adjusted by the exhaust gas fan.
Adjustments to the exhaust gas fan also influence the kiln draft. Therefore any adjustment to the exhaust gas fan normally implies also an adjustment of the tertiary air damper (or depending on the design to the kiln orifice), in order to maintain the kiln draft constant.
Only in case of separate line calciners the calciner draft can be controlled independently from the kiln through the additional exhaust gas fan.
1.2 Other control parameters
Beside the two principal control parameters temperature and oxygen and the two control variables fuel rate into the calciner and calciner draft, in certain AS designs still more adjustability is given through a staged introduction of fuel and / or meal and / or tertiary air. These design features are implemented for different reasons (e.g. NOx reduction, better ignition and burnout of low reactive fuels, refractory protection at a local hotspot, etc.). The particular adjustment of them will not be discussed within this paper.
2. GRATE COOLER CONTROL
The grate cooler is not only the most widespread type of cooler, it is also the one with the highest adaptability to the different process requirements.
2.1 Bed height and grate speed
The main objective of grate cooler operation is to recuperate the highest possible amount of energy from the hot clinker, in order to achieve a high combustion air temperature and to cool the clinker adequately.
Dependent upon the clinker granulometry a certain clinker bed height is found, at which the efficiency of recuperation is best. The grate cooler operation should try to maintain the thickness of the clinker layer on the grate constant at this optimum height.
Since this optimum thickness depends principally on the clinker granulometry, the bed height of best performance can vary over time and may change the bed height target (control parameter).
To determine the thickness of the clinker bed the following methods are used:
- Back-pressure under the first grate, if the flow of the respective cooler fan is held constant (most common method)
- Level detecting systems, working with a radar distance measurement
- Weighing systems that weigh the clinker load of a particular area, e.g. the clinker load over the fixed inlet (rarely used)
The control variable to adjust the clinker bed thickness is the speed of the cooler grate (or transport velocity of the clinker). By increasing the grate speed the clinker bed is moved out faster and the bed height is lowered. A decrease of the grate speed has the inverse effect.
Normally this grate speed is controlled automatically (mostly in function of the backpressure of one or several chambers under the first grate).
The loop, which is responsible for this control, basically has to fulfill two contrary tasks:
- quickly speed up the grate during coating falls, ring break outs and all other occasions, where the kiln releases rapidly a high amount of clinker (which requires aggressive PID settings: Proportional , Integral ¯)
- maintain under normal operating conditions the clinker bed height (i.e. the backpressure under the grate) as close to the desired setpoint as possible, without oscillation or cycling (which requires soft PID settings: Proportional ¯, Integral )
A controller, which fulfills these requirements, may have the following typical characteristics:
- Smooth grate speed adjustment, if the pressure is within a certain predefined band (e.g. 35 mbar +/- 2 mbar)
- Aggressive grate speed adjustment, if the pressure is outside the predefined band
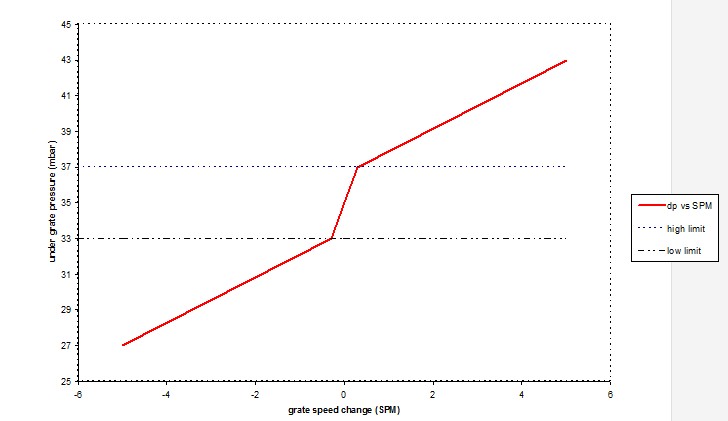
If the cooler consists of more than one grate, the speed of the following grates is held normally in a proportional ratio to the speed of the first grate. Thereby the grate speed ratio of the following grates increases gradually, thus the clinker bed height decreases stepwise from the first grate to the following ones.
1.1 Subordinate control loops
1.1.1 Cooler air flow
The flow of the cooler fans is normally automatically held constant and independent from the backpressure of the grate and clinker bed.
The objective is to provide always the same amount of cooling air to the grate, independently from minor fluctuations of the cooler throughput.
A constant airflow is a basic prerequisite to control the bed height of the clinker when the grate speed control works with the backpressure under the first grate.
The specific airflow (amount of cooling air per square meter and second) and the backpressure are highest at the first rows of the cooler and have a descending pattern towards the cooler outlet.
This is due to the fact, that the cooling of the clinker and the recuperation of the heat is as more efficient as greater the temperature difference between clinker and cooling air is. Therefore more cooling air is used at the inlet, where the clinker is still hot.
A typical air distribution (with the respective backpressures) of a cooler is shown below (in the example the cooler has 1 grate and 6 chamber aerated sections):
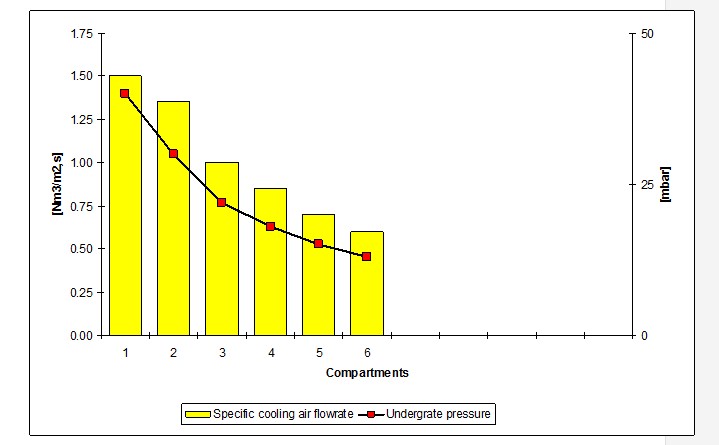
1.1.1 Kiln hood pressure
In a grate cooler, the amount of air used to cool the clinker is higher than the amount of air required for combustion in the kiln (and calciner). The surplus air has to be taken out of the cooler by a separate venting system, the so-called waste air fan.
The draft of the waste air fan has to be adjusted so that the pressure in the cooler and the kiln hood is neither positive nor too negative.
Normally this pressure is measured in the kiln hood and held constant at a value of around – 0.2 – 0.5 mbar. To decrease the kiln hood pressure (make more negative), the draft of the waste air fan is increased and vice versa.
Most frequently an automatic control takes care of this.
A constant and slightly negative kiln hood pressure is important for safety reasons and for the protection of the equipment. As the waste air fan counterbalances (pulls against) the ID fan the kiln hood pressure should not be more negative than necessary under normal operation conditions.
Nevertheless the kiln hood pressure frequently is set during start ups (cold kiln) to much lower values (– 2.0 – 3.0 mbar), in order to hold the flame back (shorten flame) and to avoid an overheating of the back end (avoid high BET due to long flame and overdrafting).
2. LEPOL GRATE CONTROL
A Lepol grate preheater basically consists of a traveling grate, which passes through two compartments. The pellets on the grate, which were formed in the pelletizer (semi dry process only), are first dried in the drying compartment and are then heated up further and partly calcined in the hot compartment.
The hot gases from the kiln penetrate the bed on the grate in the hot compartment downward, from where they are withdrawn by the intermediate fan, which controls the kiln draft.
From there they are pulled through the drying compartment by the exhaust gas fan, which controls the pressures in the drying compartment.
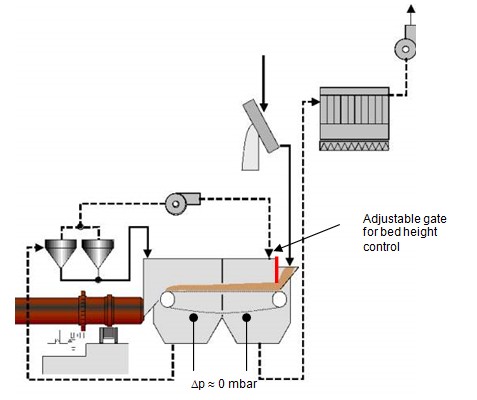
1.1 Subordinary control loops
1.1.1 Pressure control
The pressure drop over the grate in the drying and in the hot chamber is typically in the magnitude of 6 – 10 mbar, depending on the bed height on the grate and the void volume of the bed.
The size of the compartments of the Lepol preheater is designed in a way that the pressure drop over the grate in both compartments is normally equal. (Nevertheless in certain kilns, where the dust load at the kiln inlet is high, the pressure drop over the bed in the hot compartment is higher than the one in the drying compartment, due to a reduced void volume through the dust).
Since the sealing in-between the two compartments is limited it is of utmost importance to balance the pressures in between the two compartments underneath and above the grate in a proper way.
This is the task of the exhaust gas fan which is usually adjusted in a way that the pressure underneath the grate of the drying compartment is approximately equal to the pressure underneath the grate of the hot compartment (if the pressure drop over the grate in both compartments is equal then consequently also the pressure above the grate of the drying compartment must be equal to the pressure above the grate of the hot compartment).
If the exhaust fan pulls too much, the pressure in the drying compartment underneath and above the grate is more negative than in the hot compartment, which leads to a short-circuit of hot gases from the hot compartment into the drying compartment and the exhaust gas system.
This short-circuit of hot gases from the hot compartment into the drying compartment often creates a bursting of the pellets (due to an excessive water vapor pressure in the pellets).
If the exhaust fan does not pull enough, the pressure in the drying compartment underneath and above the grate is less negative than in the hot compartment, which leads to a short-circuit of “cold” gases from the drying compartment into the hot compartment and a recirculation of the gases from the drying compartment through the intermediate fan, which reduces consequently the kiln draft.
1.1.2 Traveling grate speed control
In order to guarantee a good heat exchange between gases and pellets it is important to maintain a certain bed height of the bed on the grate constant. The optimum bed height of the pellets, which is basically a function of the bed resistance must be found empirically and depends on the void volume of the bed (pellet size distribution)
The bed height is established by adjusting the passage wall between material feed chute and drying compartment (see figure 11).
The level of the material in the feed bin is held constant by adjusting the material transport to and from the pelletizer to the grate.
With increasing traveling grate speed the material feed rate increases and vice versa.
1.1.3 Pelletizer control
In semi dry kiln systems the pellets are formed from raw meal under addition of 10 – 15 % water in the pelletizer, which is just a rotating dish.
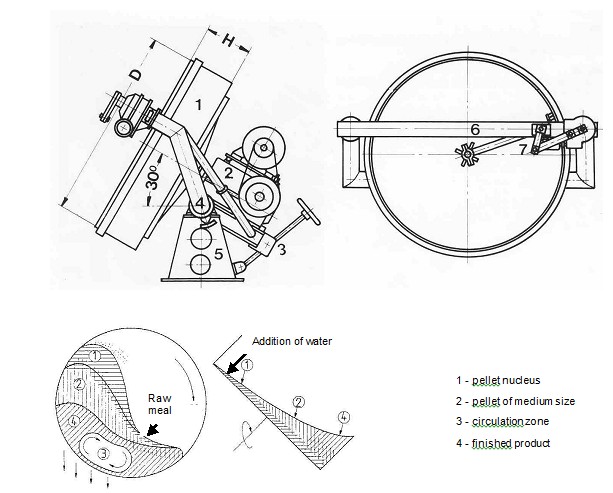
The most important properties of the pellets are size, uniformity, porosity, moisture content and strength. These properties are influenced by the raw meal feed rate (throughput), the ratio of water to raw meal (moisture content of the pellets), the angle of tilt of the dish, the speed of rotation, the height of the rim of the dish and other parameters.
From an operational point of view the raw meal feed rate (throughput) and the ratio of water to raw meal are the most important factors, which influence the properties of the pellets.
The influence of raw meal feed rate (throughput) and the ratio of water to raw meal is:
- Raw meal feed rate (at a fixed water to raw meal ratio)
The higher the raw meal feed rate, the smaller the pellet size (reduced void volume), the more porous the pellets and the less uniform the size distribution of the pellets (reduced void volume)
The lower the raw meal feed rate, the bigger the pellet size (bursting of the pellets), the less porous the pellet (bursting of the pellets) and the more uniform the size distribution of the pellets
- Ratio of water to raw meal (at a fixed raw meal feed rate)
The higher the ratio of water to raw meal, the bigger the pellet size (bursting of the pellets) and the higher the strength of the pellet
The lower the ratio of water to raw meal, the smaller the pellet size (reduced void volume) and the lower the strength of the pellet (breakage during transport)
The relation between pellet size, raw meal feed rate and ratio of water to raw meal (moisture content of the pellets) is shown qualitatively in figure 12.

In order to maintain a certain pellet size (example in figure 13), the ratio of water to raw meal (moisture content of the pellets) has to be increased slightly with higher raw meal feed rates (and vice versa).
Nevertheless the required change in the ratio of water to raw meal is small (several tenth of a percent in moisture) and a proper granulation does not simply depend on the raw meal feed rate and the ratio of water to raw meal, but is also strongly influence by the chemical and mineralogical properties of the raw meal, the design and setting of the pelletizer and a number of other factors.
1. PROCESS PROBLEMS AND KILN UPSET CONDITIONS
There are a number of unfavorable situations that require special attention and counteractions. From the great number of possible problems and upset conditions the most important ones and their respective counteractions are now presented.
1.1 Cycling
Cycling is a condition, where one or more kiln parameters (but mostly the BZT) oscillate with great amplitude around the target. This is the so-called overshooting.
An improper kiln operation itself causes quite frequently cycling, especially if the counteractions that are taken to bring back one or more control variables to target are too strong. This is a well-known phenomenon in control engineering, a general problem that exists also in other areas of control.
To inhibit a cycling of the kiln, the operation has to be smooth, i.e. any adjustment to the control variables must be as big as necessary, but as small as possible. A counteraction should consider not only on the actual condition, but also have a view to the past and future changes, i.e. beside the actual value also the trend of a certain control variable has to be considered.
To break a cycle, the kiln operation must start to counteract against one extreme of the cycle already before it gets there. When the period of the cycle is known, the counteraction for the following extreme should be taken already before the half of both extremes. This reduces the amplitude of each following cycle and brings the kiln back into stable operation.
In cycles that are caused by the kiln operation itself, the periodicity frequently is almost the same as the retention time of the material in the kiln.
In chapter 11 two formulas to calculate the retention time are given. With the knowledge of this periodicity it is possible to break a cycle early.
Beside those cycles, that can be attributed to the kiln operation other factors are also responsible. The most common ones are fluctuations of the raw material and the fuels properties. If those fluctuations have a periodic character, they may be counteracted in the same way as explained above. If they are random, the operation never will be a (counter-) action at time but always a reaction, to remedy what already happened.
Since cycling conditions have a strong negative impact on the productivity of the kiln, all efforts must be made to achieve a stable kiln operation. Therefore one of the most basic prerequisites are homogenous feed and fuel properties.
1.2 Coating Collapse
Coating is the protective layer of molten and resolidified liquid phases on the refractory in the burning zone. Dependent on the properties of the raw materials, the refractory, the fuels and the flame, this coating can be more or less pronounced.
A coating collapse is a situation, where large parts of this coating break away from the refractory in big lumps, due to excessive weight, large temperature changes in the burning zone (especially sharp temperature drops), fluctuations of the raw material properties, inadequate operation and others.
A coating collapse is detected primarily through the kiln amps. A sharp increase in the average kiln amps indicates that suddenly a higher amount of material has to be moved in the kiln. Constant spiking of the kiln amps may also indicate an uneven loss of coating in one area of the kiln.
In case a kiln camera is installed, the fallen coating can also be observed visually in the last meters before the kiln outlet. These indications help to estimate the severity of coating loss and the magnitude of counteraction that has to be made.
When coating falls out and the quantity is not too excessive, no adjustment is done to the control variables. The BZT may drop slightly for a short period but normally quickly recovers, as the coating was already closed to sintering temperature. A coating collapse results normally in elevated free CaO values of the clinker, since it is difficult to clinkerise the large pieces. For this reason no attempt should be made to clinkerise the collapsed coating, as this results only in an overheating of the entire system.
If the coating collapse is more pronounced, special attention has to be paid to the cooler, since an excessive amount of material may overfill the cooler and the clinker transport systems or lead to an excessive clinker end temperature.
If a hammer crusher is installed a close look must be given, that the coating lumps do not overload or block the crusher, otherwise the cooler grate speed has to be reduced.
When a cooler or clinker crusher overload is probable and the cooler grate speed has to be reduced significantly, the kiln should be slowed down temporarily also, in order to decrease the clinker output of the kiln and to avoid an overfilling of the cooler at the inlet. If the situation is that severe, that the kiln has to be slowed down for a longer period (longer than five minutes maximum, local equipment conditions must prevail), the fuel rate, the feed rate and the kiln draft have to be reduced.
1.3 Ring break out
In the following the counteractions after a ring break out are described.
1.3.1 Clinker ring break out
A clinker ring, which forms at the kiln outlet, is an obstacle for the clinker causing the clinker to dam up behind this ring. If this ring breaks out, an excessive amount of completely sintered clinker is released from the kiln.
A sharp increase of the cooler bed height (for grate coolers), a smooth decrease of the kiln amps and a smooth increase of the secondary air temperature indicate a break out of a clinker ring. In most cases where a kiln camera is installed, the break out of a clinker ring can be also observed visually.
For grate coolers: Due to the temporarily resulting higher output of the kiln, it is often necessary to slow down the kiln, in order to avoid an overloading of the cooler which may result in excessive clinker and waste air temperatures or a stalling of the cooler fans.
1.3.2 Sinter, middle, meal and mud rings
Each of the different ring types has its particular location and genesis (origin).
However they all have in common, that they dam up the material flow. Once a rings breaks out, an elevated amount of only partly prepared material is released. This cools down the kiln and shifts all reaction zones downwards. The kiln “pushes”.
The immediate detection of ring breakouts is difficult. Since unsintered material does not influence the kiln torque significantly, the kiln amps often do not show any change. Only if the ring was big enough that it already constituted a considerable hindrance to the gas flow, a small decrease in the pressure loss over the kiln may then be observed.
Because an immediate detection of a ring break outs is often difficult, only a sharp drop of the BZT and an suddenly increased kiln output can give rise to the suspicion that a ring has broken out earlier.
Kiln shell scanners will assist in the detection of ring formation. Likewise they can easily indicate the gradual loss of a ring. Unfortunately they will not often respond fast enough to indicate a ring collapse.
The counteractions to be taken depend on the size of the ring breakout and the general kiln condition and are most likely according to cases 1-9 of the counteractions described previously.
1.4 Hot meal rush (avalanche)
A hot meal rush or the so-called “avalanche” is a situation where the BZT drops that much that calcined but unsintered material reaches the kiln outlet. This situation may be caused by the kiln operation itself, by irregular feed advancement (e.g. ring break out, temporary cyclone blockage) or by failures of the feed or fuel feeding systems among others.
Once the hot meal has reached the kiln outlet, every effort must be made to avoid that this meal enters the cooler. Unsintered but hot meal can cause serious damage to the cooler grate.
Manual operation of the cooler may also be required if the flush reaches the cooler before corrective kiln actions can be initiated.
If the hot meal enters the cooler, a high percentage of it is blown back into the kiln. The very dusty atmosphere in the kiln inhibits a proper heat transfer of the flame towards the burning zone. Additionally the dust cools down the flame. Since nearly no heat can be recuperated from the meal, the secondary air temperature decreases.
All of these factors negatively impact the heat transfer and lead to a further drop of the BZT (but an increase of the BET).
Therefore the only, but absolute obligatory counteraction is to slow down the kiln immediately, in order to avoid dust entering the cooler and to adjust the control variables according case 1-9 of the counteractions described before.
Most likely the kiln speed has to be reduced that much that a parallel reduction of the kiln feed is not possible to avoid an overheating of the back end. In these circumstances cycling can occur.
1.5 Red spot on the kiln shell
A red spot is a locally limited area of the kiln shell that is overheated.
The shell is considered to be overheated, when the surface temperature exceeds 450°C. visible radiation on the shell surface starts at temperatures above approximately 475°C that is why it is called a red spot.
This normally comes from a worn out refractory and the lack of any coating in this area, resulting in a too high heat transfer from the inside to the outside of the kiln, due to the insufficient insulation.
High shell temperatures cause a warping of the kiln shell, which consequently inhibit proper installation of the refractory and lead to a premature failure of the bricks, due to excessive mechanical forces. Therefore they must be avoided at all times.
There are several possible reasons for a hot spot.
- When the bricks are already thin and the protective coating layer breaks away, the remaining refractory does not provide sufficient insulation. Hot spots created by this mechanism can appear from one moment to another.
- When a coating collapse occurs, the coating breaks off a layer of the refractory and weakens the brick. This may occur also as a secondary effect, when the refractory starts to crack due to the thermal shock the brick suffers, when it is exposed suddenly to the full heat of the burning zone (thermal spalling).
- All type of mechanical brick failures, where parts of the refractory fall out and leaves the shell partly or completely unprotected.
A coating loss and a local overheating of the shell may be caused by:
- A too hard burning practice, which melts away the coating and washes out the lining. The generally hot kiln transfers more heat to the shell than usual and a hot spot may occur in those areas, where the bricks were previously weak.
- Improper alignment of the burner pipe with respect to the kiln axis.
- Incorrect adjustment of axial or radial dampers, especially when too much radial air create a too broad and bushy flame.
- Snowman build-up on burner pipe which deflects air flow (or fuel) at the burner tip towards the bricks and the kiln shell.
- Poor kiln feed chemistry control resulting in periods of heavy over-burning followed by periods of under-burning.
If the hot spot is not too big (less than ~1 m2) and if it is in the burning zone, where the coating is, the kiln operator first of all should try to rebuild a protective coating layer.
A common practice is to maintain the kiln warm but to permit the calcined meal to enter periodically the affected area (e.g. by variation of the kiln speed). This cools down the concerned hot spot slightly and the meal starts to solidify and to stick over the damaged area. Nevertheless, special attention has to be paid to avoid a real cool down of the burning zone, since a cold kiln does not form coating and the following heat up during recuperation ruins the coating and the affected kiln shell even more.
In certain cases the same effect of moving the reaction zones up and down, which favors the build up of coating can be obtained by a periodic change of the temperature profile of the flame. The temperature profile is changed by regularly moving the burner into the kiln (which makes the flame longer) and out (which makes the flame shorter). Alternately the primary air settings (ratio of axial / radial air) can be changed, although this is rather not recommended.
With the correct chemistry a very slightly overheated kiln will build and maintain coating whereas a cold kiln cannot easily build or sustain coating.
An external cooling of the kiln shell in the damaged area through a fan promotes the formation of coating also. Thereby the shell temperature is reduced locally, which decreases also the temperature inside the kiln. The meal or already formed clinker will solidify more likely on the cooled area than in the hotter neighborhood.
If the mentioned measures are not effective and the situation does not improve after a certain lapse (not more than 4 h), the kiln must be shut down.
If the hot spot is bigger than ~1 m2 it is almost impossible to recover a normal shell temperature through the build-up of coating. In most case the refractory is affected already that strongly that a further detoriation of the lining through mechanical weakness is likely.
There can be also nothing done, if the red spot occurs in an area, where no coating is formed.
The common practice is then to shut down the kiln immediately and to replace the damaged refractory sections completely.
A red spot located under or adjacent to a tire is cause for immediate action. Often plant management will mandate an immediate kiln shut down.
1.6 Loss of kiln feed
A loss of feed is a situation where the kiln feed devices like feeders, auxiliary transport or extraction equipment lead to a reduction or a total loss of the kiln feed.
Since no heat is absorbed by the missing feed, the system starts to overheat, which may lead to equipment failures due to overtemperature.
Therefore the fuel rate and the kiln speed have to be reduced significantly (i.e. up to 80%). As a guideline, if the normal kiln feed cannot be restored within less than 10 minutes, the kiln has to be shut down. Tower exit temperature must be maintained below safety set points for cyclone dip tubes, downcomer, ID fan along with any additional downstream equipment. The actual temperature profile must be the guide to how fast and how severe any required adjustments are made.
2. STARTUP AND SHUTDOWN PROCEDURES
The start up and the shut down of a kiln system are the most critical phases during kiln operation. Most serious equipment failures and accidents, which are caused by the operation itself, happen usually during these two periods. Therefore special caution and attention has to be paid to the kiln system before and during start up and shut down.
2.1 Start up
When starting up a cold kiln, the general rules that have to be considered are (list not comprehensive):
- Make sure all equipment is released and cleared from maintenance people
- All vessels and risers have been inspected
- All process measurement instruments are available
- Ensure that all inspection doors and openings are closed
- The flame is supervised after lighting the burner (by a flame detector or by eye)
- The draft in the kiln is sufficient, but not excessive (overheating of the back).
- The heat up of the kiln is according a determined rate, which is given mainly by the kiln dimension and the type of refractory (normally ~50-70°C/h at the beginning, 60-90°C/h when the shell is already warm). A preheating curve is recommended. Various curves can be used depending upon several factors including type and amount of refractory replacement within the kiln system.
The kiln is periodically turned (jogged) 100 degrees, in order to avoid unbalanced heating of the kiln shell. The jogging schedule should be aligned with the preheating curve. The kiln should be turned continuously once the BET has reached 750°C (in case of heavy rain even earlier).
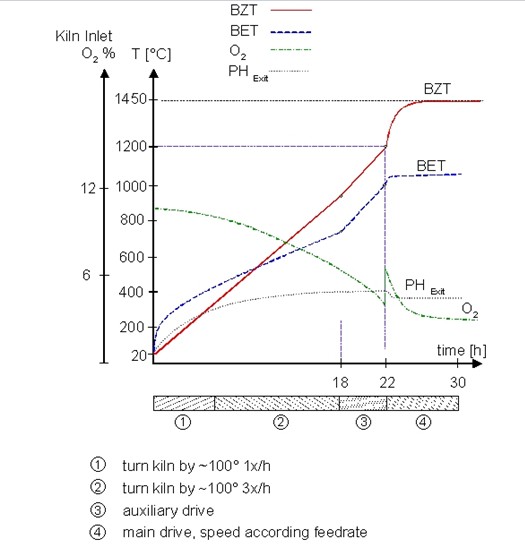
- Occasionally introducing small amounts of kiln feed during the preheat will help the bricks to set during heat up (especially, if the bricks are just installed). This will also help to prevent brick migration during periods of continuous kiln rotation.
- In case of grate coolers: make sure the first rows of the grate are covered with clinker, run the first cooler fans already during heat-up.
- In case of grate coolers: decrease (more negative) kiln hood pressure to maintain a short flame and to avoid overdrafting of the system
- In case of grate coolers: start all cooler fans before feeding the kiln. Adjust the total cooler airflow to ~2-2.5 Nm3/kg cli. Increase the cooler airflow proportionally with the kiln feed. Maintain also during start up the descending pattern of the specific air distribution, which is highest at the inlet and lowest at the outlet (graph of 7.2.1.). In many cases, the first fans reach nominal air flow already at 70 – 80% of the nominal kiln feed rate.
- In case of grate coolers: Automatic control of the cooler fans using the above setpoint guidelines, including the cooler waste air fan is desired before feeding the kiln. This will ensure sufficient air volumes for combustion.
- In case of cyclones: make sure all pendulum flaps are released and all shutoff gates are opened.
- In case of cyclones: make sure the draft is sufficient when starting to feed in order to guarantee, that the meal is not falling directly through the risers.
- Shock blasters must be online and set in the automatic mode, manual pulsing can still be initiate should the operator require it.
- Careful and close observation of the tower temperature and pressure profile must be maintained during this very critical phase of kiln operation.
1.1 Shut down
A typical shut down procedure of a kiln is (list not comprehensive):
- In case of a short-term shut down: Shut off all fuel to the system and reduce the draft in the kiln to a minimum (avoid overheating of the back and maintain the burning zone hot). However in some plants a maintenance flame is re-established in order to help maintain kiln temperature.
- In case of a long-term shut down: maintain a certain draft in the kiln but avoid overheating of the back (cool the system as fast as possible).
- Turn the kiln with the auxiliary drive for 30 minutes (in case of heavy rain fall even longer). Later on turn the kiln gradually less frequent by 100 degree, in order to avoid unbalanced cooling of the kiln shell. Unless requested for a kiln relining: do not run the kiln empty.
- In case of grate coolers: shut of the grate drive to maintain the first rows of the grate covered with clinker; leave the first cooler fans running.
- In case of cyclones: make sure all pendulum flaps are tightened and all shutoff gates are closed.
2. GENERAL CONSIDERATIONS
When operating a kiln the following general principles have to be kept in mind, which are the fundamental guidelines for proper operation.
- Protection of personnel and equipment
It is mandatory in kiln operation to avoid dangerous situations, where personnel may be injured or equipment may fail, even if a production loss or a poor quality results.
Any abnormal situation such as, but not limited to hot spots on the kiln shell, red grates in the cooler, uncontrolled hot meal rushes or fuel spillages must be prevented or remedied as soon as possible. The physical damage to the equipment that may result from an acceptance of these abnormal conditions is out of all proportion to the possible loss of clinker production that may occur from the resulting repair works.
This applies even more, if the health or life of personnel is concerned.
- Constantly good clinker quality
The aim of clinker manufacturing is to produce a clinker that is neither overburned nor underburned, since both extremes are detrimental for the cement strength. The quality, most frequently expressed as free lime content or the liter weight, should vary only in a small range.
Constant clinker quality is not only significant with view to the properties of the final product cement, but also for the following milling process (grindability, granulometry, gypsum addition, etc.).
- Smooth and stable operation
A smooth and stable kiln operation is a condition, where only very small adjustments have to be made to the kiln system.
Smooth operation is a prerequisite for a constant and uniform clinker quality.
Running a kiln in a smooth and stable manner prolongs the lifetime of the refractory as it enhances the stability of the coating in the burning zone. Both directly improve the overall productivity, since fewer kiln stops are necessary for rebricking works.
A stable kiln operation must always be preferred to a temporary maximum production that cannot be sustained.
Therefore the same emphasis that is put to push the kiln feed up should be applied to reduce it, if this is necessary.
By respecting this rule, the highest long-term productivity will be achieved.
- Maximum thermal efficiency
For economical and environmental reasons it is naturally the interest of every plant, to produce each ton of clinker with a minimum amount of fuel. Overburning the clinker, poor combustion, and unstable operation among many others prevents high fuel efficiency.
- Maximum production rate
The highest average production rate is achieved, when the kiln runs stable. Any upset condition (especially cooling of the burning zone) must be avoided.
Hence the focus must not lay only on a temporary production increase, if this provokes a cycling kiln or carries the risk of weakening (cooling off) the burning zone, since these situations imply a dramatic decrease of the feed rate and lead to a loss of overall productivity.
The feed should be increased only, if the kiln can be held fundamentally stable at a certain high production rate over some time.
3. CALCULATION OF THE RETENTION TIME
The knowledge of the retention time of the material in the kiln is of a great importance for kiln operation.
When making adjustments to the control variables, especially during cycling conditions, the retention time is in most kiln systems a guide for the reaction time of the kiln, since both are almost the same.
The retention time of the material in a dry rotary kiln can be determined mathematically in the following ways:
According Duda:
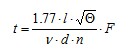
According Labahn:
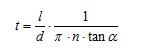
With: t: Time in minutes
l: Length of kiln in meter
q: Angle of repose in degrees: 35-40 ° for clinker 0-50 mm
n: Slope of kiln in degrees (normally 1 – 2.5 °)
a: Angle of the moved material in the kiln
(tan a must be calculated from sin a = sin n / sin q)
d: Internal diameter of the kiln in meter (in-between bricks)
n: Number of revolutions per minute
F: Factor, which equals 1, if the kiln has a constant diameter
Example:
PH Kiln with the following data:
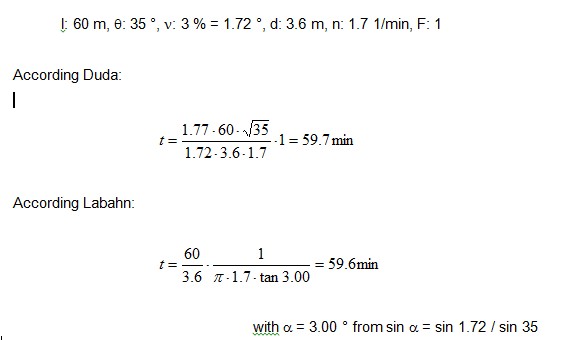
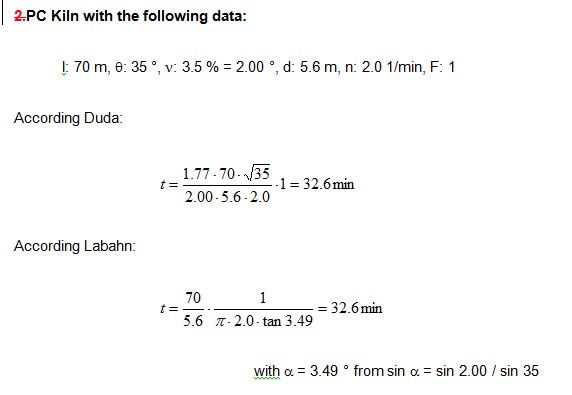
now you can be kiln Operator
EnJoy
Hi blogger ! I read your website everyday and i must say you have hi quality posts here.
Your page deserves to go viral.
Hi blogger ! I read your website everyday and i must say you have
very interesting posts here.
Very informative
Very interested.
It improve my knowledge about kils
great !!
Great webside
I must say you have high quality content here.
I read this paragraph completely on the topic of the difference of most up-to-date and earlier technologies, it’s
awesome article.
انا المهندسة اسماء شغالة فى شركة سيمكس
بحب اشكرا الادمن على المقالة الجميلة
great
thanks
thanks
I’m extremely impressed with your writing skills
i’ really more like your interesting contents & definitely, i got a deep knowledge from this your a very nice post
arvindkumar9993@gmail.com
Excellent information
Plz send this information file in my Gmail ID
Thanx
arvndkumar9993@gmail.com
Excellent information
Pls send me that information file by Gmail ID
Thanx
Excellent ! Please sent file to my email : smongpet3@gmail.com
Thank you
excelent information but expect reward from ALLAH ( S.W.T)
EXCELLENT SIR PLZ SEND ME MY MAIL
dear sir,
pl kiln operation parameter send my mail id.
thanks//regards
manoj dhakad
Verry interest. Please send to my mail
d2gam@yahoo.fr
Thanks
Excellent information sir plz send me this file at my email address.thanks
shoaibmeo786@gmail.com
Excellent information sir
Exlent
Really excellent information.It would be highly appreciated if i could receive this file at my email adress.Thanking you in anticipation Sir.
very nice information
very benifical information
plz send me information about kiln plz plz plz
Dear Sir,
Very useful information.
I request you to Please send this file to sudarshantnpl@gmail.com
exlent & helpful information
plz send this file to my mail id
bhupeshrajurkar2@gmail.com
thanking u
Great…
Plz send to me
Excellent ! Please sent file to my email : peter.slui@almatis.com
Thank you
Please send me madhu.babu422@gmail.com all PDF files
This is the most important books about cement rotary kiln I read this new year starting
Thanks for more information just send to me. Ia email pdf pls
Thanks
Dear Sir,
Very useful information.
I request you to Please send this file to demebayisa19@gmail
demebayisa19@gmail
Very good information
Thank u very much sir
please send it to me
i real appreciate a kind of knowledge and concepts from this article. God bless you.
very informationfull
Very informative content for a junior process engineer working in this kind of environment.
So understandable and briefly explained.
It’s very important information for cement industry in to make stability to the kiln .