Contents
1.1 Overview the buying criteria for Hammer Crusher
Science is the first productive force, with the continuous development of science and technology, businesses can also have rapid changes. Currently, hammer crusher has been in the cement, chemical, electric power, metallurgy and other industrial sectors are widely used for crushing various materials, such as limestone, slag, coke, coal and ore of medium hardness.
we will talk mainly around the principle of hammer crusher design, in the design process with emphasis on basic theory, structure and key operating parameters. and we will talk about the hammer crusher prices and Model selection and who are the Most reputable companies to buy the Hammer Crusher from ?
to Sum it up we will talk
- Hammer Crusher basic Theory
- Hammer Crusher Design parameters
- Hammer crusher structure
- Hammer Crusher Operating Parameters
- Hammer Crusher Maintenance and Hammer Crusher Preventive Maintenance
- where is the best Company to buy the Hammer Crusher from ?
- Buying process Criteria
- Hammer Crusher inspection.
- Advantages and Disadvantages of Hammer Crusher
1.2Hammer crusher working principle and its application
Figure 1-1 hammer crusher schematic
The basic structure of hammer crusher is shown UP.
Hammers mounted on a spindle frame.
hammer size and shape according to the specifications and material diameter crusher decision. hammer holder can swing angle of approximately 120 °.
To protect the chassis, embedded inner wall lining, fitted in the lower half of the cabinet grate bars.
Rotor shaft, hammer and hammer frame composition called the rotor.
Material are feeded into the hammer crusher, that is subject to high-speed rotation of the impact hammer is broken, crushed ore to obtain the kinetic energy of a high speed impact from the inner wall of the casing hammer at the grate, broken by the impact of the second plate crushing, as well as collision between the ore subjected to further crushing. Qualified materials crushed ore is discharged through the grate 4, the larger the material on the grate bars 4 continues to be the impact hammer, grinding and crushing, reached the required size after discharge from the gap. In order to avoid clogging comb joints, usually require no more than 10% moisture content of materials.
1.2.2Application of hammer crusher
Hammer crusher use of high-speed rotary hammer to impact the ore, In the Cement factoryit is mainly used for crushing limestone, coal, shale, chalk, gypsum and asbestos ore.
1.3 Types of Hammer Crusher
there are many kinds of hammer crusher, depending on the structural characteristics can be classified as follows:
1-according to the number of revolutions.
2- can be divided into single-axis type (or single-rotor) and two-axis (or double rotor);
3-by the platoon hammer the number can be divided into single row and multi-row;
4-according to the rotation direction of the rotor can be divided into directional and reversible type;
5-according to the hammer Movement , can be divided into fixed and movable hammers.
Hammer crusher specification is based on the diameter of the outer end of the rotor and its length dimension.
1.4 Characteristics of hammer crusher
1.4.1 Advantages of Hammer Crusher
Hammer crusher characterized by high crushing ratio (generally 10 to 25 some times up to 50), which is its greatest feature. Secondly, its structure is simple, compact size, light body weight, easy operation and maintenance. In addition, its small and uniform product size, less over crushed. Production capacity, low energy consumption per unit of product.
1.4.2 disadvantage hammer crusher
Hammer crusher working parts (such as hammer, grate, etc.) easily broken, need to be changed frequently, therefore, we need to consume more metals and downtime. In addition, the grate bars prone to clogging, especially humidity, containing clay materials, causes a significant decrease of production capacity.
Body construction hammer crusher
The design is a single rotor Φ800 × 900 mm, irreversible multi-row hinged hammer hammer crusher. It is suitable for crushing limestone, coal and gypsum or other medium hardness ore, crushing the material surface is not more than 8% moisture. This machine is gearing rotor, grate, and a framework of several parts.
Rack
it’s Cabinet the main body consist of the cover, the left and right side walls composed of various parts bolted into the wall . An upper opening a charging port, all of the inner wall of the cabinet inlaid with manganese steel liner, the liner can be replaced after wear.
Lower body is composed of 20 and 40 mm ordinary carbon steel welded bearings mounted on both sides in order to support the rotor with welded steel bearing seat.
Between the housing and the shaft, if no protective measures, ash leakage phenomenon is very serious. In order to prevent leakage of ash, usually we place shaft seal device on the casing .
Lower housing placed directly on the concrete foundation, with anchor bolts (bolt size M8 × 1000, they are 12). In order to facilitate maintenance and replacement of grate bars adjust front and rear sides of the lower frame body are opened a manhole.
The left side wall, right side wall and the rear cover, it is also welded steel plate. In order to prevent leakage of ash, , as in the local contact with the spindle side walls also have a shaft sealing device. In order to facilitate the replacement of the maintenance hammer, side walls symmetrically opened a manhole.
Rotor
The rotor is the main working part of hammer crusher.
the rotor shaft consist of hammer frame components. Hammer holder pin with a hammer . divided between three rows of hanging hammer frame, in order to prevent axial play of the hammer frame and hammers, hammer frame ends with a clamping plate and hammer lock nut . Rotor supported on two rolling bearings, bearing on a support bolted to the lower frame, in addition to the bolts, there are two locating pins fixed to the bearing center distance. Further, in order to store a kinetic energy of the rotor in operation, at one end of the spindle is provided with a flywheel. Below the structure, material, and uses several key components of the rotor to be introduced
.
Spindle support rotor hammer crusher main parts, bear the weight, impact force from the rotor, hammer, thus requiring the spindle material has high strength and toughness, the design uses a 35 silico-manganese molybdenum vanadium steel forging . Circular end surface of the spindle, the maximum diameter of 130 mm, the bearing is 80 mm. Hammer holder with b × h × L = 32 × 18 × 810 mm flat keys and shaft.
Hammer holder
Hammer hanging rack is used, it can not bear the material crushing effect, but the hammer crusher during operation, or to stand by ore hammer impact and friction caused by wear and tear, so the hammer frame also requires a certain degree of resistance grindability. The following figure shows the hammer frame is made of better steel ZG35B production, the material has good weldability, topical worn, can be repaired by welding. The hammer frame structure is relatively simple, easy to manufacture, repair and replacement more convenient.
Hammer holder Hammer holder pin hole total of 12, divided into two groups, arranged on a diameter of 490 mm and 520 mm in circumference. New for the hammer can be hung on the shaft hole diameter of 490 mm, and when the hammer wear can also continue to use, to put this somewhat worn hammer hanging in the shaft hole diameter of 520 mm and can continue to use the doing, not only can extend the life of the hammer, while maintaining hammer crusher crushing effect and reduce maintenance costs.
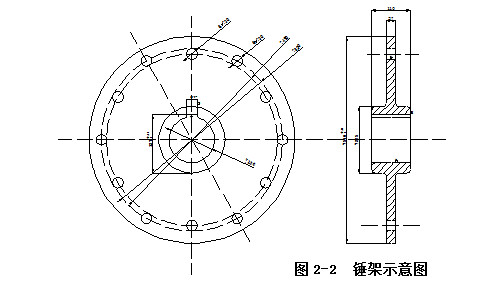
.
.
Hammer
Hammer head is the main working parts of the hammer crusher. Hammer weight, shape and material have a significant impact on the production capacity of the crusher. Proportional to the size and weight of the hammer hammer kinetic energy, namely the heavier hammer, hammer kinetic energy, the greater the higher crushing efficiency. However, the greater the weight of the hammer, spin up the greater the centrifugal force generated on other parts of hammer crusher rotor should have an impact and damage, therefore, the weight of the hammer to moderate. There are dozens of big hammer weight kg small, only a few kilograms, usually not more than 80 kg.
Hammerhead reasonable choice material is very important, ordinary carbon steel hammer heads for crushing limestone, will wear off within a few days, but with the hammer high manganese steel casting, heat treatment, surface hardening it, you can use a long time. The hammerhead materials and design used was ZGMn13 high manganese steel, a material with high wear resistance, and can withstand shock loads, suitable as hammer by its chemical composition:
Carbon (%) 0.9-1.3
Mn (%) 11.0-14.0
Silicon (%) 0.3-0.8
Phosphorus (%) ≤0.10
Sulfur (%) ≤0.05
Mechanical behavior:
Tensile strength (kg / mmCombinCombin) ≥56
Yield strength (kg / mmCombinCombin) ≥30
Elongation (%) ≥15
Shrinkage (%) ≥15
Brinell hardness 179-229 HBS
Impact value (kg.m/mm2) 3
Hammer on the shaft hole, as shown. Because of poor high manganese steel machinability, so the casting is required prior to discharge φ30 × 5 mm seamless steel pipe, if the error is not cast, not processed can be placed in the hammer frame. If the deviation is large, it can be reused after processing, generally do not need reworking. The hammer symmetrical shape design, so when one side after the wear and tear, can be used upside down. But when the hammer badly worn, difficult to repair and therefore, the use of new replacement of worn hammer crusher to maintain normal production. In addition, if the individual was more powerful hammer wear, the rotor will be out of balance, job insecurity crusher, can also lead to premature wear of the pad. Therefore, the production should always pay attention to the hammer wear, timely inspection, periodic replacement of the hammer.
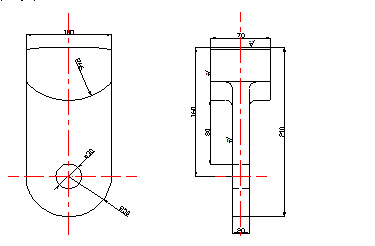
.
Flywheel
The main role is to make the flywheel rotor crusher in operation stored in a certain kinetic energy, while maintaining the efficiency of the crusher at work, reduce the power consumption of the crusher. That is, when the normal operation of the crusher, the flywheel will store some energy, the motor is not caused by overload, when the crusher into the feed too much or chunks, put the flywheel kinetic energy release, and enhance crushing capacity, so that the electric motor without overloading run, play a protective role.
Kinetic energy stored in the form of hammer crusher, in different ways differ, if the drive mode using a pulley or V-belt pulleys, eliminates the need to configure the flywheel, pulleys itself played a role in storing kinetic energy, direct drive if the drive mode using the electric motor, then you should consider another configuration flywheel to increase the kinetic energy reserves.
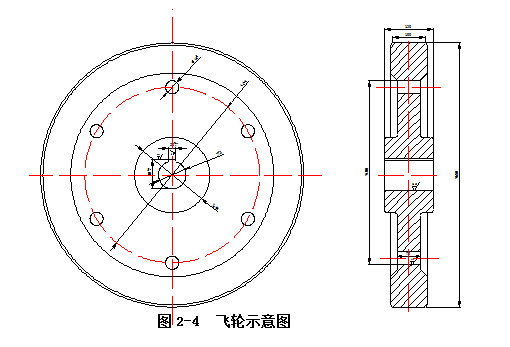
.
.
.
grate
Arrangement grate hammer crusher is perpendicular to the direction of movement of the hammer, and the radius of gyration of the rotor arc-shaped certain gap. Qualified products can grate seam, the seam is greater than the grate material because it is not through the crack and grate on grate and then subjected to the impact hammer and abrasive continue to be broken, and so on until the volume was reduced to crack through the grate. Grate and hammer as severely impact and abrasion, easy to wear is one of the main parts. Grate bars by hard material or chip of metal impact, easy to bend and break. As shown in FIG, Φ800 × 900 hammer crusher grate bars, its shape is substantially trapezoidal cross section, made of high manganese steel ZGMn13, with high wear resistance, can withstand the shock loading. Grate grate gap is projected portion is formed.

.
.
.
.
pallets and lining
Hammer crusher with high-speed hammer hammering ore, ore in an instant with a great speed, in order to prevent wear of the rack, the rack is fitted in the inner wall of manganese steel liner.
And other components from the pallet and backing plate assembly and became a hit. Pallet is welded with ordinary steel, above all liner high manganese steel castings, with hammer and grate of the same material. After assembled with two shaft holder on the body frame of the crusher, the feed angle can be used to adjust the adjustment screw, can be replaced when worn severely, in order to ensure product quality.
Table 2-1 alloy composition and heat treatment
C | Mn | Si | P | Mo | Cr | Heat Treatment | |
A | 1.1 ~ 1.40 | 5.0 to 7.0 | <0.8 | <0.04 | 0.8 to 1.2 | _____ | Normalizing, hardening the surface |
B | 0.90 to 1.1 | 13.0 to 15.0 | <1.0 | <0.05 | ____ | _____ | Normalizing, hardening the surface |
C | 1.1 to 1.25 | 12. to 14.0 | _____ | _____ | ______ | ____ | ______ |
D | 1.1 ~ 1.30 | 12. to 14.0 | ______ | _____ | ____ | 1.6-2.1 | ____ |
E | 0.8 to 1.00 | 12. to 14.0 | ______ | ______ | 0.9 to 1.1 | _____ | ____ |
F | 1.1 to 1.25 | 12. to 14.0 | <1.0 | _____ | 1.8-2.2 | _____ | ____ |
G | 1.2 ~ 1.35 | 12. to 14.0 | <1.0 | _____ | ______ | _____ | _____ |
H | 12. to 14.0 | 12. to 15.5 | <1.0 | _____ | ______ | _____ | Dispersion hardening |
2% molybdenum high-manganese steel for high yield strength without lowering the toughness of high manganese steel castings, such as the initial broken shield, molybdenum 2% manganese by high dispersion treatment, has sufficient toughness, its service life than 2% molybdenum conventional high manganese steel heat treatment to 25 percent. But the dispersion treatment of high production costs, limiting its use. 1% molybdenum, 0.8 to 1.0% carbon-high manganese steel with high toughness and strength, the use of normalized surface hardening heat treatment cost is not high. Therefore, in this design, I use 1% molybdenum, 0.8 to 1.0% of the carbon-containing high-manganese steel as the liner.
overload protection device
Metal to hammer crusher is a great threat, in order to prevent the metal into the crusher caused by accident, hammer crusher generally have safety devices. When equipped with safety copper sleeve on the shaft hammer crusher, pulley set in copper sleeve, copper sleeve with the pulley is connected with the safety pin when the internal hammer crusher into the metal or overload, namely pins and cut protection. The design uses a shear pin safety coupling, when the crusher severely overloaded affect its performance, namely shear pin coupling on and play a protective role.
Dust seal
The purpose of sealing to prevent dust and water from entering the bearing and relative movement between the components, such as gears meshing roller at the same time play a role in preventing the loss of lubricant. Seal is good or bad directly affects the rolling bearing and gear roller life, thus affecting the efficiency of the whole machine.
Due to inclement hammer crusher working environment, we need a good seal sealing device, the traditional felt seal device has been unable to meet the requirements of this design uses a labyrinth sealing method, the axial clearance is 2.5 mm, 0.5 mm for the radial and grease is pressed into the labyrinth passage, in order to improve the sealing effect.
Selection and calculation of structural parameters and operating parameters
rotor diameter and length
(1) The diameter of the rotor is generally based on the size of the ore to decide. Typically the rotor diameter to the size of the ore block ratio of 4 to 8, a large crusher is approximated to 2. Since Φ800 × 900 hammer crusher for medium crushing machine, so to diameter ratio of the size of the ore block to take 7, and processed material size ≤120 mm.
Therefore, the rotor diameter D = 6 × 120 = 720mm, D = 800mm take
(2) depending on the length of the rotor machine capacity may be. The ratio of the rotor diameter and length is generally 0.7 to 1.5, ore impact resistance is strong, should choose a larger ratio. Because due Φ800 × 900 hammer crusher mineral processing for such a number of medium hardness ore limestone, coal or gypsum, so take the ratio of 1.1.
The rotor length L = D × 1.1 = 800 × 1.1 = 880mm, Take L = 900mm.
determine the size of the basic structure
1, to the mine mouth width and length: hammer crusher to the mine mouth width B> 3dmax, dmaxIt represents the maximum size of the ore block to. B> 3dmax =4 × 120 = 480mm, take B = 500mm, while the same length of the feed opening and rotor length, so they chose to spout length L1 = 900mm.
Rotor Speed
To simplify the design, hammer crusher no gearbox. Therefore, the crusher rotor speed and the rated speed of the motor is installed the same. The rotor speed is controlled by the peripheral speed of the hammer. Rotor speed is an important parameter impact crusher, the rotor speed can be calculated by the following formula:
n=60v/3.14D r/min
Wherein the circumferential velocity v —- the rotor;
D —- diameter of the rotor;
Rotor circumferential speed v can be broken according to the nature of the ore is calculated:
v=0.01× (9.8/r)0.5 G0-5/6/E1/3 m/s;
Where: g —– gravitational acceleration, g=981cm/s2;
r —– ore denisty, kg / cm3;
G0—- Ore compressive strength, kg / cm2;
Modulus of elasticity E —- ore, kg / cm2;
Since the formula did not reflect the reduction ratio of this factor, the rotor circumferential speed is calculated according to the rotor speed is only as a reference. Currently, the use of the peripheral speed of the rotor hammer crusher is 15 ~ 80m / s, generally, when crushing takes 15 ~ 40m / s, taking 40 ~ 80m / s when finely divided. Although the higher rotor speed, the greater the reduction ratio, but also hammer wear faster, the power consumption is also large. Therefore, in efforts to meet the requirements of the situation, the circumferential speed of the rotor should be low. By the above analysis shows that:
n = 60v / 3.14D (here v take 40m / s)
= 60 × 44 / 3.14 × 0.8
= 987.7r / min
In order to reduce the wear and power consumption, take
n = 980r / min
Productivity
Currently, hammer crusher has not been considered a theoretical formula of various factors, so we use empirical formulas to calculate.
Our crushing medium hardness materials to calculate the productivity of hammer crusher:
Empirical formula: Q = (30-45) DL * δ (t / h)
Where: D —– diameter of the rotor, unit: m;
L —– rotor length, unit: m;
Loose proportion δ —- ore unit: t / m3
Because of this design D = 800mm = 0.8m;
L = 900mm = 0.9m;
Loose denissty ore δ take 1.62;
Formula coefficient of median 38;
Then Q = 38 × 0.8 × 0.9 × 1.62 = 44.324 t / h.
According to the results, we can determine the Φ800 × 900 hammer crusher production rate of 44 tons / hour.
Motor Power
Hammer crusher power consumption related to many factors, but mainly depends on the nature of the ore, the circumferential speed of the rotor, crushing ratio and production capacity.
Currently, the motor power hammer crusher yet a complete theory formula, usually based on production practices and the use of experimental data or empirical formula to select the motor power Crusher.
According to the actual production practices to select motor power:
N = KQ (KW)
Where: Q — machine production capacity, t / h
K — than power, kW / ton, compared with the power consumption depending on the material to be broken nature of the structural characteristics of the machine and the reduction ratio may be. Of medium hardness limestone hammer crusher take K = 1.4 ~ 2. When crushing small to take, when to take larger crushing.
This design requires a finely divided mineral, and therefore larger than the power selected
(Take K = 1.7 kW / t), Q = 44.32 t / h;
Then N = KQ = 44.32 × 1.7 = 75.14≈75 KW.
According to the results of the calculation motor power, integrated requirements, look-up table to select Y series (IP23) three-phase asynchronous motors (JB / T 5271-1991,5272-1991). Model Y280S-6. Motor efficiency of 92%, rated current of 143A.
rotor speed and the weight of the hammer
Hammer crusher rotor speed n and hammer weight G are interrelated. Hammer crusher is not seen by all the energy to swing broken material, but only broken by the hammer of moving work to do to complete the material. E is the kinetic energy of the hammer:
E=mv2/2 …………………………………… (3-1)
Where E —– hammer kinetic energy, J;
Mass m —– hammer, kg;
Circumferential velocity V —– hammer, m / s.
V=(πDn)/60 …………………………………… (3-2)
Wherein n —— rotor speed, r / min;
D —— when the rotor rotates, centrifugal force, radially hammer, then the outer diameter of the rotor on the side to D (m) represents.
The formula (2) into equation (1) to give
E=(mπ2D2n2)/7200 N.m …………………… (3-3)
Proportional to the size and weight of the hammer hammer kinetic energy, namely the heavier the hammer, the greater the kinetic energy of the hammer, the higher crushing efficiency, but the greater the weight of the hammer, spin up the greater the centrifugal force of a hammer other parts of the crusher rotor should have an impact, and speed up the damage, therefore, the weight of the hammer should not be too heavy nor too light to moderate.
The right choice hammer crushing effect on the weight and energy consumption has a great influence. So choose must meet the weight of the hammer hammering at once so that the material block broken and useless power consumption to a minimum, must also not to bias the hammer back down. Therefore, we must make the hammer in motion equal to the kinetic energy generated by crushing the material needed to combat power.
As shown in equation (3) below:
All rotor hammer once per revolution generated by the kinetic energy Eafor
Ea=k1k2E=( mπ2D2n2k1k2)/7200 N.m ……………… (3-4)
Formulas k1 ——– Number hammer row of rotor circumferential direction
The number of each transverse row of rotor hammer
k2 ——–
Na kinetic rotor rpm per minute n all hammer produced as follows:
Na=(nEa)/(1000×60)=( mπ2D2n2 k1k2)/(1000×60×7200)kw ………… (3-5)
Due to the uneven and loose than the feed material, the actual, not all can be the name of the material hammer, hammer some empty too. Therefore, the equation (5) do not have to be multiplied by feeding uneven and loose material factor.
Na all kinetic energy produced per minute hammer is supplied directly by the motor, so that the formula (5) with the power N of the motor is equal to emitted per minute, can be considered against all the crushing hammer can be produced by the process material. that is:
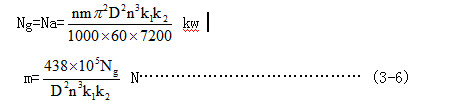
Formulas: Motor Power Ng ………… hammer crusher, kw (Ng take 75kw);
D ………… hammer crusher rotor diameter, m, (D = 0.8m);
k1 ………… speed of the rotor in the circumferential direction of the hammer row, k1= 6;
k2 ………… transverse rotor hammer each row number, k2= 8;
n ………… hammer crusher speed, n = 980 r / min.
m == ≈3.5kg
Equation (6) just consider all the kinetic energy of the hammer in motion can break the material, and after the hammer blow and did not consider the material, the size of its rate of loss, if the fight against material, the speed loss is too large, it would Rao hammerhead own suspension axis rotation without breaking the material, which will reduce production capacity hammer crusher and increasing exercise in futility. Of course, the hammer blow of material generated by the centrifugal force deflection can be restored to its original position, but must return to normal position before the second blow material. Therefore, the only allowed after the hammer blow material loss rate of 40% to 60%, starting from the principle of equal kinetic energy can be obtained:
GV = (G1 + G) V2 Unit: Nm / sec.
V2 = [G / (G1 + G)] V …………………… (3-7)
Where: G —- converted to the weight of the hammer blow at the center, N
G1 —— largest block of material by weight, N
—– Hammer peripheral speed against the V start possessed, m / s
Equation (7) is equal to the coefficient of 0.6 to 0.4 i.e.
V2 = (0.6 ~ 0.4) V m / s ……………… (3-8)
By the formula (7) obtained:
GV = GV2 + G1V2
G = G1 ×((v2)/(v-v2)) N ……………… (3-9)
The formula (8) into (9)
G = G1 × = (0.7 ~ 1.5) G1
Among them, the largest block of material mass m = ρ × v = 3.63 × 12CombinCombin= 6272.64g = 6.273Kg
(Density ρ take 3.63g / cmCombinCombin)
G1 = mg = 6.273 × 9.8 = 61.4719≈61N
Hammer weight G = (0.7-1.5) G1 = 42.7-91.5N
G Take 75N
hammer crusher drive program
To make the hammer crusher rotor kinetic energy stored in a certain operation, to avoid crushing bulk materials, the speed of the hammer will not lose too much and decreasing the peak load motor at one end of the spindle must be configured to use a pulley and flywheel or connected to the motor. The total design considered three drive programs, namely: 1. The end of the spindle with V pulley connected to the motor; 2 using coupling one end of the spindle motor connected to the other end of the configuration of the flywheel; using spindle 3 at one end V pulley and the motor connected to the other end and then configure the flywheel.
Comparison of these three methods, since this design is a small and medium sized crusher, its kinetic energy does not have to store large pulley itself stored kinetic energy can play a role, it is not necessary to configure the pulley at one end and the other end then configure the flywheel, so it should first abandon the first three kinds of programs. So now we look at the first and second programs.
First look at the first option, according to the motor power and rotor speed, we can choose the motor model Y280S-4 (rated power 75KW, full load speed 1480r / min), the following, we designed based on these raw data V-belt drive
1) Calculate the power Pc, was the work of Richard coefficient from Table 5.5 KA = 1.5, so
Pc = KAP = 1.5× 75 = 112.5 KW
2). Select the V-belt type, according to Pc = 112.5KW, n1 = 1480 r / min, is determined by the choice of type C in Figure 5.14.
3) Determine the reference pulley diameter D1 and D2, taken from Table 5.6 D1 = 600mm, ε = 1%, by the formula
taken from Table 5.6 D2 = 900mm, large pulley speed
4). Checking the tape speed v
Since the tape speed too high, the centrifugal force increases, the positive pressure belt and pulley transmission is decreased and an ability to reduce, and affect the life of the belt, the belt speed is in the range of 5-25m / s, and We need to adjust the small pulley diameter of 300mm or less, and a large pulley diameter to be adjusted to 450mm or less, so that due to the large pulley diameter is too small, and the V pulley design is to try to make a small mass, structure, technology is good, therefore it can not meet its kinetic energy storage role, at the other end must also configure the flywheel.
To sum up, the drive to finalize the program for the configuration suitable flywheel shaft at one end and the other end is connected with the coupling and motor.
Design calculations of hammer crusher main parts
5.1.1 Spindle Design
For only pass circular section shaft torque, the strength conditions:
τ = T / ZP = [(9.55 × 106P) /0.2d3n] ≤ [τ] N / mm2
Where:
Twisted effective force τ- axis, N / mm2
T- torque N / mm2
Zp- polar section modulus, d3Circular cross-section of the shaft:
Zp = πd3/16≈0.2 D3
P- transfer of power, kw
n- spindle speed. r / min
[Τ] – allowable torsional shear stress, N / mm2
For both torque transfer and withstand bending moment axis diameter formula available on preliminary estimates axis; but you must promise to use the shaft torsional shear stress [τ] be appropriately reduced to compensate for the bending moment on the shaft. Xu will reduce stress after substituting into the above equation, and rewrite the formula for the design
Where A = 98 ~ 107 Because of the design of the spindle material 35SiMn, and bear a large load, high bending moments. So take A 107
And because P = 75KW n = 980r / min
Taking into account the crusher is exposed to changes in torque and impact loads vary greatly, the take-up shaft finest at dmin = 70mm
The strength of the fine conditions at the shaft as follows:
Look-up table 35SiMn allowable torsional shear stress [τ] = 40 ~ 52 N / mm2
τ = 10.6N / mm2 <[τ]
That strength at 70mm thin shaft conditions meet the strength requirements.
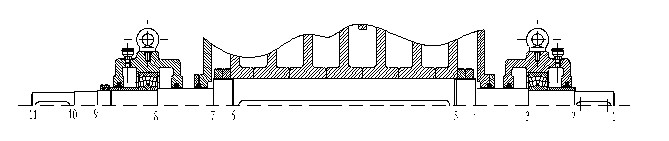
.
The minimum diameter of the shaft is installed at the flywheel shaft diameterIn order to make the coupling shaft diameter and pore size selected to adapt it to simultaneously select Coupling Model. Coupling torque calculation Tca = KAT, look-up table 10.1, taking KA = 2.3, then: Tca = 2.3 × 730867 = 1589994 N.mm.
According to the calculated torque should be less than the nominal coupling torque condition, check standard GB / T 5843-86 or manual selection of a shear pin safety coupling, aperture coupling halves Ⅰ of d1 = 71mm, so they chose d1-2 = 71mm, coupling half length L = 132mm, the hub bore and the shaft with length L1 = 107mm. In order to meet even half the shaft axial positioning requirements, 1-2 axis segment should be made out of a left shoulder, so take the 2-3 segment diameter d2-3 = 80mm, L1-2 = 104mm.
At the same time due to the bearing by radial and axial force, and the spindle is subjected to a large torque and is subject to shock loads, use double row spherical roller bearings, with reference to job requirements and in accordance with d2-3 = 80mm, the choice of roller bearing 22316, d × D × B = 80 × 170 × 58, using the left shoulder axially positioned, the shoulder height h = 5mm, taking d3-4
= 90mm, with sleeve positioned between right and couplings. Sets the length L = 48mm. Roller bearing width B = 33mm
To make reliable clamping sleeve bearings, take L2-3 = 79mm, bearing housing width of 120mm, the outer wall of the cabinet to cabinet distance 35mm, casing wall thickness 20mm, taking a manufacturing error s = 10mm, so it chose L3-4 = 133mm.
Rotor disc with the sleeve clamping position, take the shoulder height h = 10mm, then d5-6 = 130mm, for reliable compression rotor disc, take L5-6 = 896mm.
Since the symmetrical arrangement of bearings, still take L6-7 = 40mm, d6-7 = 110mm, L7-8 = 133mm, d7-8 = 90mm, bearing sleeve and collar positioned, since the leftmost configuration flywheels, flywheel hub a length of 130mm, the flywheel will not make contact with the cabinet, taking the flywheel and the bearing housing distance of 160mm, the L8-9 = 150mm, take L9-10 = 120mm, d9-10 = 76mm, left with a flywheel shaft gear collar, flywheel hub diameter of 70mm, so they chose d10-11 = 71mm, L10-11 = 125mm.
Coupling halves, the rotor disc, flywheel and shaft are made of circumferential positioning flat key links. Coupling half and the coupling shaft, use the flat key is b × h × L = 20 × 12 × 90mm (GB1096-79), with the coupling half and the shaft is H7 / k6 shaft of the rotor disc and circumferential Since positioning is longer than 500mm, according to GB / T321-1980 “priority number and priority number system”The R20 series, select L = 810mm, b × h = 32 × 18mm; coupled flywheel and shaft, use the flat key is b × h × L = 20 × 12 × 110mm.
5.1.2 Spindle strength check
First made in accordance with the structure of the shaft axis calculation diagram, since the hammer crusher to withstand impact loads at work, and this impact load is concentrated in the hammer blow of the material, in order to facilitate the calculation, the load will now be reduced to the role of the rotor on the uniform load. Assuming the material in a hammer collision angle (α <)
Consider the use of stress margin coefficient e = 1.5 (so-called margin coefficient, that is, the deviation in the compensation load, estimated inaccuracy, approximation of the dimensional accuracy of the error and the formula at the same time, the result of vibration, shock generated difficult to predict the rise in stress, residual stress prediction inaccuracy coefficient compensation), the force acting on the hammer on each are as follows:
.
.
hammer crusher operation and maintenance
7.1 Hammer Crusher basic operation of law
7.1.1 before starting hammer crusher should do the preparatory work:
- Crusher main parts: such as hammer, broken boards, doors and check fastening bolts is intact. Loose.
- Carefully check the auxiliary equipment such as feeding devices, couplings, motors and other equipment are in good condition.
- Whether the debris crushing cavity, if found to have lumps or metal objects in the crushing chamber, should be cleared.
- Check the amount of oil carried.
- After doing the above work, issued a driving signal, in order to obtain power after the next step agreed.
7.1.2 Start Notes on Operation
- After doing the above preparations, you can start the crusher and motor, then should control the current.
- After the crusher is operating normally, you can start feeding equipment, material fed to the crusher, and the crusher according to the size and functioning of the gob, adjust the volume of feed feeder, such as a large block of material, the crusher when the materials are more appropriate to reduce the volume of feed will have, on the contrary increase the volume of feed, usually the height of the material in the crushing chamber should not exceed 2/3 of the height of the crushing chamber.
- The operation should be noted that even feeding, this will help increase production of crushing, while the size of the material is not too large, they should be controlled 120mm or less, so as not to cause hammerhead stall.
- To prevent the hard processes with sharp metal objects into the crushing chamber, so as to avoid damage to the hammer and other parts of the grate bars.
- After the automatic tripping of electrical equipment, if unexplained, non-forcible consecutive starts.
- Equipment operation, to carry out inspection tours, such as found in the following circumstances, should immediately stop work
A bearing temperature higher than 70oC
B found abnormal sound.
7.1.3 Parking Precautions
We must stop the production process, which is to stop feeding, and other materials and then stopped working after all the broken crusher.
To prepare and clean up after the shutdown Check the machine’s various parts, carefully prepare equipment production records.
7.2 Security technique
7.2.1 holding protective devices and alarm devices intact
One is to protect the safety of life, such as safety hood and grille flywheel and transmission device, feeding railing around the mouth. The other is used to protect the machine itself, so often referred to as the hammer crusher safety device.
7.2.2 Operation and maintenance PRECAUTIONS
- In strict accordance with the startup sequence to start the device.
- Moving the case should be preceded by checking equipment around the availability of Xianzarenyuan.
- Must start signal before driving.
- Equipment operation is prohibited across the railing into the spout.
- Equipment operation, do not touch the rotating swing member.
- Equipment operation, do not leave the job or do other things.
- Wet hands inhibit operation of electrical equipment, electrical equipment should be grounded wire.
- Overhaul must be cut off the power, and the listing represents.
- Lifting weights, following strictly prohibited.
10, when dealing with the crusher blockage prohibiting people standing on hand to dig up material bulk materials, preferably with a stick or a special hook like.
11, after the repair, move, or remove safety devices should be restored to the rear drive.
7.3 Hammer crusher maintenance law
7.3.1 Lubrication
Lubrication can reduce friction and reduce wear and tear parts, strengthen equipment lubrication equipment maintenance is a very important way.
For each of the rear bearing lubrication should work eight hours, filling a lubricating oil to the bearing. Change the oil every three months. Oil change, should be cleaned bearing with clean kerosene.
7.3.2 mobile inspection and routine maintenance
- Check bearing fever, the temperature does not exceed 70oC.
- Check bearings, oil change whether the need to refuel.
- Check the bolts connecting the flywheel is loose.
- Check that the lubrication system is working properly, if that is not enough oil, should be supplemented.
- Keep cleaning equipment, especially in the lubricated components and lubrication systems.
- Regular cleaning with gasoline lubricating oil filters, after cleaning to wait to continue using dry completely.
7, regular replacement of oil can be changed every six months.in conclusion
In this design the three-month period, I never learned a profound understanding of design issues hammer crusher ,, knowledge learned in four years of our university, especially for mechanical design, mechanical principles, mechanical and knowledge of cartography have a deeper understanding and awareness. And from the ability to develop their own independent thinking and problem analysis issues, and information retrieval capabilities for literature, but also cultivate we will learn the basic theory and professional knowledge to use the ability to solve practical problems. To develop our ability to work independently and innovation have a very important role. Of course, there are also many good and does not solve the problem needs to be improved and enhanced in these processes. Although the design will inevitably be inadequate, but through this exercise for my future career success has laid a solid foundation. The design has been able to successfully accomplish this is with the careful guidance Song teachers are inseparable, and in the design process has been eager to help two students of the same group, in this very grateful to them, especially to thank Song teacher in the past few months on my careful guidance so I successfully complete the graduation project. Of course, this design is certainly not perfect, in the design of many shortcomings, hope the teacher can give criticism